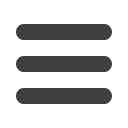

News
Technology
November 2016
46
www.read-eurowire.comNDC
Technologies’
Beta
LaserMike
LayScan gauging system offers cable
manufacturers an accurate and consistent
method to measure the lay length of
twisted pairs in data communication
cables, such as Cat 5e/6/6a/7a/8 products.
LayScan solves scrap, costly rework and
productivity loss problems due to manual,
time-consuming lay length measurement
methods and crosstalk performance
issues from lay variations.
LayScan can be used to measure the
four pairs at the cabler or to measure an
individual pair at a twinner to confirm
the accuracy of twisted-pair cable
construction during production.
This non-contact system uses up to four
individual pair lay sensors and the Beta
LaserMike LaserSpeed® length and speed
gauge to perform the high-speed lay
length measurements. A data acquisition
and control system effectively collects
and processes each lay length in the cable
and allows the full use of the customer’s
off-line analysis tools such as trend
charts, statistical analysis or FFT analysis
to readily observe, measure and report
systematic lay variations within each lay.
Data can be easily stored on a local
PC. LayScan measures lay lengths up
to 25.4mm at throughput speeds up
to 152.4m/min with a measurement
accuracy to within 0.025mm on the same
twisted pair.
LayScan can be used in conjunction with
the Beta LaserMike SRL Pro structural
return loss measurement system for a
total on-line cable performance quality
solution.
SRL Pro can be used before and/or after
the extruder to identify potential causes
of structural return loss problems on data
communication cables.
NDC Technologies – USA
Website
:
www.ndc.com/betalasermikeSince 1923 Ideal has stood for innovation
and progress in the production of
welding machines and automation,
including
custom-made
machine
solutions according to customers’ specific
requirements.
The German company manufactures
mesh welding machines, coil joining of
wires and stranded conductors, as well
as welders for grating, fencing and the
production of wire articles such as cable
trays, covers, frames, rings, etc.
The fence market is changing. Until a few
years ago standard fences were produced
in large numbers. Today, the lot size is
much smaller and the focus is on the
quick changeover of welding machines.
Adapting
to
the
ever-growing
competitive pressure and the flexible
manufacture of superior products are
now more than ever central issues. In the
procurement of welding machines for
the production of fences, high-quality
welding, automation, resource-saving
production, as well as flexibility and
minimal set-up are at the top of the
requirement profile.
In order to respond flexibly towards
different requirements of manufacturers
and markets, Ideal offers various
manufacturing
concepts
and
configurations:
•
GA-Series
wire
mesh
welding
machines for the production of small
to large lot sizes, from simple to
complex fencing mesh – for single
and double wire fencing mesh and
3-5-8 security fencing mesh
•
CSR Versaweld
TM
jig welding machines
for the flexible production of small
batches and special mats for a variety
of fencing mesh and decorative
fencing
•
Accessories
for
the
individual
configuration of the machines
•
Bending presses for automated
V-shaped bends in 3D fencing mesh
•
FSD production lines for the fully
automated
production
process,
available
in
different
versions
depending on the product portfolio;
for the manufacturing of complex
products and large quantities (eg,
for single and double wire fencing
mesh, 3-5-8 security fencing mesh, 3D
fencing mesh, decorative fencing, as
well as customised solutions)
One of the most important aspects of the
modular design is the fact that modules
in existing installations can be retrofitted.
This allows for the machines to grow
with the demands of the markets and the
requirements of the manufacturers.
An adaptation to the welding task is
realised by way of complex welding
cylinders, different transformer versions
(AC alternate current, DC single-phase
current, 1,000Hz medium frequency
technology), as well as the possibility of
direct and indirect welds and a variety of
process-related options.
The classic cross wire weld is subject
to much higher quality requirements.
In a ‘bad’ weld with a burr that is too
pronounced, moisture collects at the
cross point.
A subsequent powder coating creates
bubbles in which trapped moisture
causes
the
cross
point
to
rust.
Subsequently, the hydrogen-induced
cracking causes corrosion of the welds
and consequences similar to those of
material fatigue.
To rule out such errors and in order to
meet the required quality standards, Ideal
offers not only the appropriate hardware
and software, but also the individual
welding expertise based on almost 100
years of experience.
Ideal-Werk C+ E Jungeblodt GmbH + Co
KG – Germany
Website
:
www.ideal-werk.comAccurately measure lay length at cabler and
twinner
▲
▲
The LayScan gauging system offers accuracy and
consistency
Innovation and progress from Ideal-Werk
▲
▲
FSD fence line welding portal