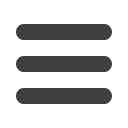

News
Technology
November 2016
47
www.read-eurowire.comB&H Tool Company, of California, USA, a designer and
manufacturer of high quality, custom plastic extrusion tooling,
has added Computational Fluid Dynamics (CFD) analysis to its
portfolio of approaches for optimising and designing annular dies
for plastic extrusion.
The flow simulation analysis software is completely integrated
with its computer-aided design and manufacturing software to
ensure high-quality tooling.
“Management’s strategy is to bring the same approach to annular
dies such as crosshead, in-line and co-extrusion dies, for single
layer and co-extrusion applications. We want to bring the same
technology that worked in film and sheet dies to annular die
design,”said Peter Neville, B&H’s managing partner.
With CFD, B&H’s team of experts design and manufacture annular
dies that deliver uniform polymer flow to the exit of the die. The
process starts with two required inputs: polymer rheology and a
target output rate. With those inputs, designers can go to work
to design a head assembly customised around a customer’s
application.
If a customer has multiple applications, B&H’s engineering team
can help them determine where they want their target output rate
to be.
Analysing their output rates (as a function of pounds per hour) has
been a big step forward for companies, Mr Neville reports. In
many instances, across all industries, companies have not been
looking at their tooling as an area of improvement.
With the multitude of challenges faced in the manufacturing
sector of both the USA and global economies, manufacturers
have often been trying to use a ‘one-size-fits-all’ approach
to their tooling capacity. CFD helps companies look at their
tooling from a different perspective and help them straighten
out their tooling. Often companies have developed ‘bandaids’
to compensate for uneven flow in their tooling.
With CFD, B&H’s designers are able to simulate (before any
metal is cut) polymer flow at a target out rate. With optimised
tooling (as a function of pressure, velocity and shear),
manufacturers can then focus on dialling in on the dimensions
and quality of their products.
Companies report faster start-ups and can operate with
less-skilled operators because they are not ‘fighting’ the tooling
as much. With operations in lesser developed countries or
competitive industries, these can be significant issues.
CFD is used for all types of annular dies – adjustable centre,
fixed centre, co-extrusion, in-line and in-line spiderless dies.
The approach is the same, as the goal is to deliver even flow
to the exit of the die. Once the software inputs have been
finalised and the tooling has been optimised using CFD, B&H’s
team reviews the final design with the customer and goes over
the simulation. Once the customer has signed off on the final
design, then the job is ready to be sent to production. Since
they have been involved in the process, the customer is able
to integrate the tooling more efficiently once it lands on their
receiving docks.
CFD analysis is helpful in today’s more sophisticated plastic
extrusion applications or high volume, low margin applications.
Whether it is low output micro-bore tubing, insulated fine wire,
multi-layer automotive tubing or multi-layer irrigation tubing, CFD
ensures that the tooling is optimised for the application.
For example, in irrigation tubing, post consumer polymers
are used to bring down the cost of the tubing. Using CFD to
make sure the rheology of ‘regrind’ is taken into consideration
ensures that a major issue is addressed. In the case of low output
applications, making sure the volume is optimised and the
appropriate deflector is used is critical.
B&HTool Company – USA Website
:
www.bhtool.comTool maker brings flow simulation analysis
technology to crosshead
Jiangsu Qunye Electrical Co., Ltd.
is a specialized spools
manufacturer. We have highlevel workshops and offices, first
class equipment lines and complete inspection facilities, advanced
management and quality control systems to fulfill all customers’
requirements. We manufacture all kinds of
metal and plastic spools and gain a good
market share both at home and abroad.
▲
▲
Simulation analysis to ensure tooling is optimised for the application