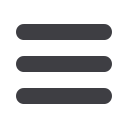

J
anuary
2009
www.read-tpt.com28
T
echnology
U
pdate
›
Economical cladding based on hot wire TIG welding
Polysoude, France, has developed an economical system using hot wire TIG welding
for cladding applications. The technology is designed to address the costly problems
of pipelines that transport oil or natural gas according to high speed and high pressure.
High quality materials are
required to resist sand and
other abrasive minerals, or
corrosive materials.
Pipe and pipe component
manufacturers
improve
the inner surface of pipes
by a welding technique
called cladding. During
this operation, the interior
of the pipe (made from
inexpensive black steel)
is reinforced by a layer
of Inconel, an extremely
resistant material.
Polysoude has become a specialist in this area, with exports to Europe, Asia and the
Middle East. Orders for the welding system exceeded several million Euros in 2008.
Polysoude
– France
Fax
: +33 240 681 188 •
:
info@polysoude.com•
Website
:
www.polysoude.comRapid and intuitive scanning to test curved parts
Manufacturers of tubes and fittings can improve the inside surfaces
of their products by cladding with wear-resistant Inconel alloy
Sonatest’s 50mm array Wheelprobe
Sonatest Ltd has launched its new
Wheelprobe
™
series of probes. Developed
in conjunction with leaders in aerospace
technology, with a focus on the increased
use of composite materials, the probes
enable rapid and intuitive scanning in the
testing environment, producing quantitative
data on material integrity.
The probes feature a wide, comfortable
rubber tyre that is acoustically matched to
water, allowing near dry contact, and so
produce high quality results without the
need for couplant or large quantities of
water.
The Wheelprobe range includes three
models: a single element model, and 50mm
and 100mm array versions. Developed to
be used in conjunction with the Sonatest
Rapidscan series, they are compatible
with alternative NDT industry standard
equipment.
The 50mm array Wheelprobe is suited
to hand scanning of large, flat or slightly
curved parts, covering such areas quickly
and efficiently. A central spring-loaded
roller ensures consistent contact across
the wheel, even when scanning narrow
parts. The Wheelprobe is able to provide
high quality, high-resolution data due to
the incorporated 64 element phased array
with 0.8mm resolution and a high resolution
positioning encoder.
The 100mm tyre has been constructed for
very large area coverage and due to its size
is best suited to flat horizontal components,
but is also adaptable to curved parts.
Industry sectors where the Wheelprobe may
be used include aerospace, automotive,
marine and composite manufacturing.
Adaptable for use by individual operators
or as part of a scanning system, the
Wheelprobe is suited to advanced material
testing, simplifying testing procedures
and preparation where there are common
requirements for the ultrasonic inspection
of composites for porosity sizing,
delaminations, foreign body contamination
and fibre wrinkling.
Sonatest Ltd
– UK
Fax
: +44 1908 321323
:
sales@sonatest.comWebsite
:
www.sonatest.comHigh frequency induction
heating system for
reduced energy costs
Cheltenham Induction Heating Ltd, an
Ambrell company, has announced the
expansion of the Ekoheat line of induction
heating systems to 135kW, designed to
deliver energy savings to the heating
phases of manufacturing processes.
Ekoheat technology reduces energy usage,
compared to alternative heating methods
such as gas-fired ovens and resistive heating
techniques. With efficient power conversion
and a power factor greater than 0.9, utility
demand charges are significantly reduced,
resulting in lower monthly energy bills.
Flameless, non-contact induction heating
also minimises energy waste by focusing
energy only on the zone to be heated.
Ekoheat systems are suited to case
hardening, high-speed brazing, melting,
crystal growing, continuous wire and
continuous strip heating. The systems
deliver reliable solutions for larger parts of
many geometries and compositions. The
Ekoheat is designed for the worldwide
market, supporting 360 to 520 AC line
voltages, and is CE marked.
The user-friendly control interface, available
in six languages (English, Spanish, French,
German, Italian and Polish), streamlines
operator interactions and provides valuable
runtime information.
The expansion of the Ekoheat series
adds 65kW, 90kW and 135kW units to
the existing 15kW to 45kW models, at
operating frequencies from 50kHz to
150kHz. Additional models at higher power
levels and with a wider range of frequencies
will also be available. The range of products
is manufactured at the ISO 9001:2000
certified Ameritherm facility.
Cheltenham Induction Heating Ltd
– UK
Fax
: +44 1242 224146
:
sales@cihinduction.comWebsite
:
www.ambrell.com