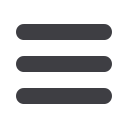

J
anuary
2009
www.read-tpt.com30
T
echnology
U
pdate
›
3M has launched three new air-powered
metal finishing tools – a disc sander, a die
grinder and a cut-off wheel tool, comprising
eleven variants. All are equipped with
powerful high-output air motors, and are
designed to optimise tool and abrasive
performance and incorporate measures
to increase and enhance operator
usability and comfort. These include 360°
directional exhausts and 3M’s patented
Greptile material (on most of the tools),
a surface covering manufactured using a
micro-replication process pioneered by 3M
that provides a more effective grip while
requiring less effort from the operator.
The disc sander features a 97° head angle,
greatly increasing the ergonomics of the
tool, and promoting a more comfortable wrist
position for the operator. The tool’s easier-
handling, lightweight, compact design also
generates less vibration, allowing improved
overall operator control. The disc sander is
available in three variants: two 2" models
with different airflow and power ratings
(0.33HP and 0.5HP), and a 3" version
offering 1HP. The unit’s powerful air motor
allows jobs to be completed faster, and a
smaller head means users can work closer
to the surface being abraded, allowing
better access, control and visibility.
The disc sander’s Quick-Attach system
swiftly connects it to 3M’s range of Roloc
metal finishing consumables. This allows
the sanders to be fine-tuned for a wide
array of applications, including deburring,
grinding, blending, finishing and cleaning.
From Roloc coated abrasives and Scotch-
Brite discs to everyday general-purpose
aluminium oxide discs, users can match
the tool and consumable to the application’s
requirements. A range of back-up pads is
available in different diameters and degrees
of hardness.
3M’s new pneumatic die grinders have
been designed to efficiently handle
refining, finishing, cleaning and deburring
needs on the complex production parts.
Four models are available with different
rpm ratings (8, 12, 18 and 20,000). All
feature a powerful 1HP motor, allowing
users to complete jobs quickly, and the
unit’s advanced ergonomic design gives
greater control during operation. Operator
comfort is further enhanced with directional
exhausts and Greptile grips. A wide range
of 3M consumables, including Scotch-Brite
brushes and wheels, bristle discs and
flap wheels, means that the die grinders
are suitable for applications using a wide
variety of metals, from basic carbon steel to
titanium.
The company’s new 1HP cut-off wheel tools
share the same ergonomic features as the
other models, but also incorporate additional
built-in safety features, including a safety
lever throttle and a 360° rotatable safety
guard. The range consists of four models:
3" and 4" wheel in-line units and 4.5" and
5" wheel right-angle units. Designed to offer
performance and dependability, users have
a choice of 3M’s Cubitron Abrasive grain
wheels (available in 3" and 4"), or Inox
aluminium oxide wheels (available in 4.5"
and 5").
3M Abrasive Systems
– UK
Fax
: +44 1612 371106
:
abrasives.uk@mmm.comWebsite
:
www.3m.com/uk/abrasivesUser, tool and abrasive in perfect harmony
The high tension and mandrel retraction
force of more than 100kN make it possible
to form thick-walled tubes safely, reliably
wiping wrinkles. The Z axis is displaced
to allow for automatic calibration of
the bending height. The system auto-
matically stores programmed bending
options and tool data, which can be
retrieved at the touch of a button. All
processes are controlled by Siemens
840D software.
Tube bender with automatic tool changeover
The new, fully automated Silfax tube bending
machine for wide diameter pipes up to 127mm,
with automated tool changeover
Machine manufacturer Silfax, France, has
launched a fully electric CNC tube bender.
The SE 9127 is designed for large diameter
tubes and piping, and offers a variety of
bending height options.
The system is controlled by Siemens control
technology, making it suitable for fully
automated bending of larger pipes under
safe working conditions. The SE 9127 is
also the first machine of its type to offer
automated tool changeovers, and simplifies
fully automated production with a mix of
interfaces and cell integration.
The SE 9127 is equipped with nine electric
CNC-controlled axes and is capable of
bending pipes up to 127mm in diameter.
Tool changing is fully automated and the
system can be fitted with four top-of-the-
range tools for tensioning and gripping
pipes with inflections or reduced holding
areas.
“
Although it’s more effort at first than a
hydraulic system, we tension the pipes
electrically,
” explained Thomas Rohde,
head of systems technology at Silfax, “
but
the results speak for themselves: bends are
extremely accurate and can be reproduced
time after time.
”
There is strong demand, particularly in the
aerospace industry and in the automotive
sector, to bend large diameter, thin-walled
tubes safely and accurately. Other areas
where every millimetre counts and pipe
tolerances must be kept to an absolute
minimum include truck exhaust systems
and intermediate components used in
hydroforming processes.
The new Silfax machine works along
seven linear axes down to 0.05mm. During
bending and forming it is accurate to 0.05°.
To keep cycle times to a minimum, the SE
9127 offers feed rates of up to 30m/min.
Bending and twisting can be carried out at
up to 62rpm.
The SE 9127 incorporates interfaces for
RS232, RS422, and ethernet, making it
suitable for connecting to external systems.
Integrating cells into bus networks is also
easy. The system can be tailored to specific
requirements, with options including wiper
dies, an automatic mandrel device and
machine bed extensions. Silfax is already
planning the introduction of its next machine,
for pipes up to 157mm in diameter.
Silfax
– France
Fax
: +33 4 7231 0619
:
info@silfax.comWebsite
:
www.silfax.com