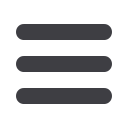

May 2017
MODERN MINING
47
feature
CRUSHING, SCREENING
AND MILLING
M
ultotec Manufacturing's Pro
duct Manager Screening,
Shawn Faba, believes that
Multotec’s composite deck
systems have taken screening
technology to another level. “By applying the
science of stratification, we ensure we can de-
sign a screen that produces the size and speci-
fication of output required by the customer;
we then also engage in ‘the art of screening’ by
meticulously fine tuning the process through
monitoring and iteration that leverages our
market-leading Hawkeye technology,” he says.
“We differentiate ourselves by the in-depth
way we use our Deck Map methodology to
design and optimise solutions, based on the
characteristics of the material being treated.
This also allows us to adapt our solution to the
dynamic nature of orebodies, which leads to
constant changes in the material to be treated,
even in the same orebodies.”
The ‘deck map’ is the guide to the planning,
design and fine tuning of the composite deck,
allowing the best combination of panels to be
placed to suit the conditions, the material and
the output targets. With decades of experience
in screen panel manufacture, Multotec pro-
duces a wide variety of purpose specific panel
types, from materials including rubber, poly-
urethane, steel, woven-wire, ceramics, Hardox,
fibreglass and combinations of these materials.
“The deck map allows us to specify, for
instance, a set of panels comprising highly
impact resistant material at the feed end of the
screen, where the impact of material from the
feed box or chute is highest,” says Roy Roche,
Vice President Screening Media at Multotec.
Choices might include Multotec’s RubCer
wear product manufactured with both rub-
ber and ceramic elements; the extremely
hard ceramic surface provides exceptional
resistance to wear and cutting, while the rub-
ber’s elastic properties dampen the impact
forces and protect the
ceramic pieces.
Alternatively, the
commodity and application may be best suited
by the RubMet product, in which Hardox
500 sections are embedded in rubber. Plates
designed with small Hardox blocks are more
suitable for medium to large particles, while
those with strips of Hardox work best for large
ore particle applications.
“One deck might comprise over a dozen dif-
ferent types of panels, and each one is there
for a very specific reason,” says Roche. “The
apertures will be chosen according to the
screen’s purpose and factors like the feed ton-
nage required, the average particle size and the
particle shape; we cater for the full range of
screening applications such as scalping, des-
liming, dewatering and sizing.”
To cater for all these demands, in just about
every commodity mined globally, Multotec’s
panel offerings include solid feed-end panels,
slope change panels, slotted aperture panels for
high velocity zones, and square aperture panels
for low velocity zones depending on bed depth
and cut size.
A key requirement in screening is also to
Composite deck systems
take screening to a new level
Seen here in discussion are
Shawn Faba (left) , Product
Manager Screening at
Multotec Manufacturing,
and Roy Roche, Vice
President Screening Media
at Multotec.
Shawn Faba examines a
Losiplast panel, which is
suitable for heavy duty
applications.
While the concept of composite decks, which comprise
panels of various materials, apertures and configurations, is
not new, screening media specialist Multotec has, for over a
decade, developed the added value that this approach can
bring to a customer’s bottom line.