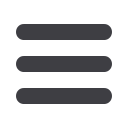

Technology News
www.read-tpt.comJ
uly
2015
29
Complex forms with reduced tooling
THE demands for tube processing are
increasing. Geometry is becoming
increasingly complex and materials are
becoming ever stronger in connection
with progressively light design. At the
same time there are calls for efficiency
across all sectors.
Rolling tube forming by transfluid
is a process that opens up special
opportunities for forming and reduces
the use of tools to a minimum. Rolling
technology displays its strengths most
clearly if forming is to be carried out on
tubes that have already been axially
preformed, if sharp edged contours
need to be created for sealing elements,
or if perfect surfaces are required.
For tool-independent tube forming
and for the creation of almost freely
formed geometries, all transfluid t form
bead rolling machines have a servo-
electric drive and an easily operated
CNC control system, if required. This
allows the functions of different axes to
be moved in an overlapping fashion. As
all the setting parameters are stored,
there are no complex adjustments and
this saves valuable time. The forming
process is possible both from outside
to inside and from inside to outside.
A further advantage of rolling tube
forming is that even completely different
geometries can be formed with a single
tool, a clamping jaw and the rolling head.
Tool wear is almost totally eliminated in
a rolling process, and the lubricants that
are necessary in the forming process
can be reduced to a minimum.
If demanding forming is necessary on
high-strength materials, a closed rolling
head is used. The forming rollers are
completely supported within this. The
forming of highly complex geometries
without space in the axial direction is
carried out using three rollers that are
included in an open structure. This
means that the roller geometry can be
carried out directly on a tube/flange
connection.
It is also possible to roll threads or
add edge designs with the same roller
head and the corresponding rollers,
with or without forming, depending on
requirements. Trimming of already-bent
components can also be realised by
rolling tube forming without cutting and
almost without burrs.
If complex geometries need to be
formed almost without clamping length
then a roller head takes over this
role, allowing the rolling or separating
process across two rollers. One roller
is positioned as support on the inside
or outside of the tube while the counter
roller delivers the form. This kind of
inner support or forming roller can be
used from an internal tube diameter
of 12mm, whereby very different tool
pairings can be used. For example, this
makes it possible to form and separate
simultaneously.
Another advantage of this technology
is the surface quality that is created by
the forming. It is usually possible to do
without a cost-intensive form clamping
piece on tubes that have already been
bent, because of the low loads that are
transferred to the tube during the rolling
process.
transfluid Maschinenbau GmbH
–
Germany
Fax: +49 2972 9715 11
Email:
info@transfluid.deWebsite:
www.tube-processing-machines.comA groove contour
on a hose
connection
The t form SRM 622 tube forming machine allows
the creation of almost freely formed geometries
Fully automated sawing solutions
KENT Automation, a division of
MNM Mfg Inc, is an engineering and
manufacturing company that offers a
full range of innovative, customised and
fully automated sawing solutions.
Recently the company supplied a
double head mitre saw with pneumatic
positioning of angles via a selector
switch.
Currently Kent Automation is in the
design phases of a multi-head cutting
and milling machining centre for one of
the world’s largest composite fabricators.
The equipment will be installed at its
Canadian operations. This machine will
be designed to mill and saw five styles
of profiles at one time. There are four
machines in total and they will be fully
automated with an HMI touch screen
for setup, monitoring and running the
machine.
Since the early 1990s KentAutomation
has supplied several thousand individual
cutting and milling-related machines.
Kent Automation
– USA
Website:
www.kentautomation.com