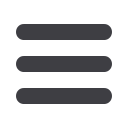

Technology News
www.read-tpt.com34
J
uly
2015
Multi-Cut efficiency
from Austria
AUSTRIAN machinery specialist
Linsinger has produced its popular tube
cut-off machine-series Multi-Cut for
many years.
Managers responsible for service and
maintenance in tube mills often find
that machines need to be repaired and
improved more than suppliers some-
times claim when they originally pur-
chased the machine. This is something
Linsinger specifically works to avoid.
“We plugged in the Linsinger Multi-Cut
and it has been running from the first
minute,” said the manager responsible
for the maintenance department of the
German tube specialist Mannesmann
Line Pipe MLP in Hamm.
The Linsinger tube cut-off machine
was first installed in 2004 and has
worked continuously since then without
a problem.
The construction and installation of
the cut-off machine into an existing
pipe production line was a smooth
process with the help of Linsinger and
its technicians.
The 50-ton machine has shown its
pedigree from the beginning. With low
tool costs and optimised saw blade life
the Multi-Cut MC 4-610 cuts the burr-
free inner and outer edges of longitudinal
welded tubes in an
exceptionally fast time.
A logical develop-
ment of the Linsinger
cut-off machine Multi-
Cut MC4, which works
with four independent
controlled drive assem-
blies, is the Multi-Cut
tube cut-off machine
MC3, which helped
to revolutionise tube
cutting with cross-
section
dimensions
of between 150 and
660mm. The stationary
tube cut-off machine
MC3 is particularly suited to the
sampling of tubes’ respective endcuts,
and is deployed both for welded tubes
and seamless tube mills.
It possesses three smaller circular
saws, which are fixed on a radial
revolvable disc and deliver a tidy, ready-
for-sale cut.
Considerable shorter length of
cycle results from the simultaneous
engagement of all three saws in the
tube and the rotation about 120°; the
pure cutting time for a P110 steel tube of
dimension 244 x 13.5mm is about eight
seconds.
Another essential advantage is that
if one saw fails, the machine is able to
continue the work without interruption to
the schedule or changing of the sawing
blade.
Furthermore, the cutting time can
be synchronised optimally to the
sawblades, which benefits the cost
effectiveness of the machine.
Compared to the larger and more
expensive sawblades of conventional
steel circular saws, the Multi-Cut
machine can be used with smaller and
less expensively priced sawblades.
When combined with the longer
durability of the smaller sawblades
this results in a reduction of the tooling
costs, which, after often more than 20
years in use, clearly carry more weight
than the costs for the machine itself.
The MC3 also features fully automated
tool changing, which is performed by
a robot as soon as a certain number
of cuts have been made. The robot
changes all three sawblades in only
90 seconds. Over the lifecycle of the
machines of approximately 20 years this
can help to save more than half a year
during three-shift operation.
“Not only through accuracy but also
due to its cost effectiveness the MC3 is
state-of-the-art. The additional charge
compared with conventional saws
amortise within two to three years,” said
Linsinger-CEO Hans Knoll, when he
summarised the multiple advantages
that many customers worldwide have
enjoyed.
The tube cut-off machines, Multi-Cut
MC3 and MC4 from Linsinger, Austria
have made tube cutting technology
faster, more efficient and more
economical.
Linsinger Maschinenbau GmbH
–
Austria
Fax: +43 7613 8840 951
Email:
maschinenbau@linsinger.comWebsite:
www.linsinger.com