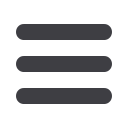

Technology News
www.read-tpt.com36
J
uly
2015
Induction heating for
oil country tubular goods
Aurélien Lechoisne of EFD Induction
outlines the benefits of using induction
heating for pre-heating and stress
relieving tubes and casing destined for
the world’s toughest environments.
OIL country tubular goods (OCTG)
refers to tubing and casing meeting the
specifications of API 5CT. Although the
standard states that API 5CT pipe may
be made by the seamless or electric
resistance welding (ERW) process,
the reality is that OCTG typically refers
to seamless threaded pipe. OCTG
also includes seamless and ERW
transmission pipe that carries media
such as oil, gas and water, conforming
to API 5L standard.
The diameter of a pipe’s end must be
reduced or expanded prior to threading.
This change in diameter is achieved
by swaging, a process that introduces
additional stresses into the pipe end. Left
untreated, such stresses render pipe
ends brittle, making them susceptible to
deformation.
Two heat-treatment methods are
used to overcome this problem: the
first involves avoiding the stresses
altogether by pre-heating the pipe end
prior to swaging; the second method
involves removing the stresses by
‘stress relieving’ after swaging.
Various heating technologies exist
for bringing the pipe ends to the
temperatures needed in both methods.
Induction heating, however, has the
ability to meet four criteria critical to
OCTG manufacturers in today’s hyper-
competitive market.
Firstly, induction heating is extremely
accurate. Target temperatures and heat
penetration depths can be reached and
maintained for very specific areas for
exact time periods. Secondly, induction
heating is highly productive. Because
heating occurs only in narrowly defined
zones, no time is wasted heating
adjacent areas or the ambient air.
Thirdly, induction heating is extremely
controllable. This makes it suitable for
maintaining temperatures within pre-
determined narrow tolerances. Finally,
induction heating – by virtue of its speed
and accuracy – confines the heat to the
pipe end. The induction heating process
is simply too quick and controllable for
unwanted heat transfer to occur along
the pipe.
The benefits mentioned above are
due in large part to induction heating
producing heat in the wall of the
pipe end itself. This fundamental fact
not only contributes to the speed of
induction heating, but also makes it a
no-contact technology – a feature that
helps minimise the risk of unwanted
interference or contamination of the pipe
end.
Another crucial factor is customisation.
As induction coils are available in a
practically unlimited range of designs,
the actual heating process can be
optimised to the specific composition,
dimensions and requirements of
particular work pieces.
Coils are only one element in an
induction heating system. The other
key component is the heat source (also
referred to as generator or converter, as
it converts the mains supply into the high
frequency supplied to the coil). Today’s
solid-state induction heating systems
typically feature the actual generator –
those used in EFD Induction systems
feature Sinac units – as well as matching
and cooling equipment. Power ratings
and frequency ranges vary widely.
For example, EFD Induction has to-
date built systems for pipe ends with
outer diameters as small as 60.33mm
(2
3
/
8
") with a wall thickness of 4.83mm
(0.19"), up to an outer diameter of
558.8mm (22") with a wall thickness of
23.42mm (0.92").
The particular features of an induction
heating solution will
vary from supplier to
supplier, but there are
some points of differ-
ence that merit careful
consideration.
One such factor
is the use of ‘flux
concentrators’ with the
coil.
Concentrators are components that
focus, or concentrate, the heat into
particular areas of the work piece.
Undoubtedly beneficial in other induction
heating applications, their use in pipe
end heat treatment is questionable. This
is because concentrators are relatively
short lived, and must be replaced at
regular intervals – leading to production
shutdowns and additional costs.
Concentrators
can,
however,
be dispensed with if good quality
customised coils are used – preferably
coils designed using advanced
simulation software.
The saving delivered by maximised
uptime and output soon recovers any
additional capital outlay caused by using
such coils.
A final argument in induction heating’s
favour is its track record. A tried-and-
tested method, induction heating for
OCTG heat treatment is a technology
currently in worldwide use. EFD
Induction, for instance, has devised and
built systems for some of the leading
names in the tube and pipe industry.
Induction heating, thanks to its high
efficiency and absence of toxic by-
products, helps manufacturers satisfy
tough environmental and energy-
consumption regulations – not a bad
bonus when making products needed
to meet the world’s growing energy
demands.
EFD Induction
–
Email:
sales@efdgroup.netWebsite:
www.efd-induction.comInduction heating for
OCTG heat treatment
is a technology
currently in worldwide
use