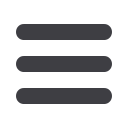

Technology News
www.read-tpt.comJ
uly
2015
67
EXCELLENT QUALITY
INNOVATION
EXPERI ENCE FOR MORE THAN 100 YEARS
GLOBAL NETWORK
FOR THE BEST RESULTS IN CUTTING
ANY SIZE OF BLADE FOR ALL MACHINES
MADE IN JAPAN
since 1910
TCT-CIRCULAR SAW BLADES FOR CUTTING BAR/TUBE/PIPE
TENRYU SAW MFG. CO., LTD.
| Japan, Fukuroi,
www.tenryu-saw.comTENRYU EUROPE GMBH
| Germany, Aalen,
www.tenryu.deTENRYU AMERICA INC.
| USA, Hebron KY,
www.tenryu.comTENRYU SAW DE MEXICO, S.A. DE C.V.
| México, Silao, Guanajuato,
www.tenryu.mxTENRYU (CHINA) SAW MFG. CO., LTD.
| P.R. of China, Langfang, Hebei,
www.tenryu.cnTENRYU SAW (THAILAND) CO., LTD.
| Thail., Amiphur P., Rayong,
www.tenryu-saw.comTENRYU SAW INDIA PVT. LTD.
| India, Neemrama, Rajasthan,
www.tenryu-saw.com. . . ASK TENRYU
!
Thread protection in 20 seconds
COMPANIES seeking an alternative
between tedious manual operations
for applying pipe thread protectors and
expensive robot automation can now
choose a new customised product from
Automation Engineering Company LLC.
AEC’s automatic thread protector
applicator is based on the principles of
a mechanical compliant system that can
handle a variety of thread protectors,
providing precision torque within a
20-second takt time (or less), and can
handle pipe from 2.5" (63.5mm) to
13
5
/
8
" (350mm) in diameter.
“Pipe ends are not always perfectly
perpendicular or aligned, so we’ve
designed a system that adjusts to the
pipe angle a couple of degrees in any
direction,” said AEC president Manfred
Gollent. “We use all-electric controls so
it moves forward exactly to the pitch of
the thread.”
Protective caps are fed into the
automatic thread protector applicator
using a de-palletiser capable of full-
height pallets. The de-palletiser loads
with a slim profile pallet jack or forklift.
Fully automated, thread protectors are
fed row-by-row into a chute ready to be
picked up for application.
To accommodate different pipe sizes,
the thread protector system adjusts
vertically during changeovers. The pipe
itself never moves. The only manual
interference occurs when grippers and
cradles are changed to accommodate
pipe sizes. Changeover to a different size
of pipe takes less than ten minutes.
Unlike other systems that currently rely
on robots for applying thread protectors
on tube and pipe, AEC’s solution requires
lower investment and comes with an
automated doping system. In addition,
an automatic, vision-based inspection
system provides assurance that the pipe
end is threaded and doping is applied
correctly. The inspection process can
identify if a pipe has a reject stripe and,
therefore, skip the protector application.
“It’s a very cost-effective solution
that allows pipe mills to reduce pipe-
to-pipe cycle times,” Mr Gollent said
of AEC’s automatic thread protector
applicator. “We continue to take proven
technologies and designs and apply
them in new and creative ways.”
Automation Engineering Company
LLC
– USA
Website:
www.teamaec.com