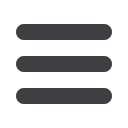

Equipment
Pipel ine Inspect ion
54
Tube Products International April 2008
www.read-tpi.comthe right-of-way. Blocks can be full
body or made from a section of the
cut from the pipe, depending on the
customer’s specifications. Scan
Systems Corporation also manufactures
and sells through EDM Specialties two
models of portable electric discharge
machines designed to fabricate flaws
in all types of metal products. It also
offers a line of electromagnetic (EMI)
pipe inspection equipment through its
PITCO Division. The portable Tally-Rite
measuring equipment is also marketed
by Scan Systems Corporation.
Scan Systems Corporation
– USA
davids@scansystems.com www.scansystems.comMag meter
measures liquids
down to 0.1µS/cm
An ultra-compact electromagnetic
flowmeter has been launched in the
UK by mass flow metering and control
technology specialist, Bronkhorst UK.
Also available with an integral PID
controller for flow control duties, the
Miniature-Mag series is suitable for
measuring liquids with a low conductivity
down to 5 microSiemens/cm, even as
low as 0.1µS/cm for some applications,
and for handling flow rates between
1 litre/hr and 3,000 l/hr.
Intended mainly for smaller bore
installationsandcapableofbeingusedon
pipework bends rather than just straight
runs, it is available for internal pipe
diameters between 1.5mm and 12mm
and features empty meter detection for
when there is insufficient flow. The very
high speed of response makes it suitable
for batching applications, a capability
further enhanced by automatic overrun
compensation.
Unlike standard magnetic flowmeters
that require electrodes to be placed
within the fluid path, often clogging
up with sticky substances, Miniature-
Mag sensors do not restrict the flow
path, giving 100% full bore flow. This
combination of features makes it
suitable for many industrial and hygiene-
ScanSystemsCorporation,USA,through
its operating division EDM Specialties,
manufactures custom calibration blocks
for automatic ultrasonic inspection
(AUT) equipment designed for pipeline
girth weld inspections.
Each block is manufactured to
customer’s specifications, provided with
engineering drawings. The blocks are
cut from lengths of pipe samples sent
by the customer that are job specific as
well as equipment specific. The blocks
are fabricated to match the design of
the inspection equipment. All reflectors
in a block are measured and certified,
and qualified third party inspectors are
available.
Blocks can be mounted on custom
dummy rings made of a lighter material
than the pipe for easier handling on
Phased array scarf monitoring system
GESensing& InspectionTechnologies,USA,
has introduced a weld profile visualisation
system using phased array technology. This
new scarf monitoring system provides a
real time, accurate picture, on-line, of both
the ID and the OD profiles of scarfed ERW
pipes, as scarfing takes place. As a result,
it is possible to effect real time control of
the scarfing process, by identifying events
such as tool drift and edging as they occur.
This can achieve significant reductions in
scrap.
The heart of the new system is the
ultrasonic phased array transducer, which
electronically simulates the scanning
action required to provide the weld profile
information.
The resultant information is then fed into the UTxx digital flaw detection
platform. This incorporates standard or phased array flaw detection channels
and all the associated processing electronics, to give a complete scarf
monitoring and flaw inspection package. In operation, the transducer test head
assembly is mounted such that it is directly above the weld line. The mill coolant
acts as the ultrasonic coupling medium. The transducer test head then uses its
phased array elements to monitor the inside and outside diameter of the weld
as it is being cut, at a scanning rate of up to 300 profiles/sec. Transducers and
shoes are available to monitor tubes from 50 to 500mm in diameter and typical
coverage is ±25mm from the nominal weld centre line.
Inspection data is displayed in true-to-scale cross-sectional profile at one or
multiple monitor screens, and high and low limit alarms provide warning of weld
profile deviation. Intelligent dynamic software averaging techniques minimise
the possibility of false readings.
The weld profile visualisation system features all-electronic set-up for ease of
use and repeatability, and it can be installed within feet of the weld station,
depending on local temperature conditions. As a result, it operates both as a
process control system and a quality control system. It can be combined with a
flaw detection system, and allows inspection traceability through a built-in data
logger, which records minimum and maximum thickness readings across the
weld area and strip thickness.
GE Sensing & Inspection Technologies
– USA
www.ge.comGE’s new scarf monitoring system
S
S
Custom pipeline girth weld calibration blocks