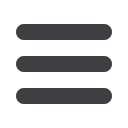

56
Tube Products International April 2008
www.read-tpi.comEquipment
Pipel ine Inspect ion
Girth weld pipeline inspection system
GE Inspection Technologies, a business unit of GE Enterprise Solutions,
has announced the release of Weldstar, a complete, automated ultrasonic
girth weld inspection system for oil and gas transmission pipelines. Weldstar
provides gains in productivity and probability of detection, without the hazards
associated with ionising radiation, when compared with traditional film-based
radiographic non-destructive testing.
Weldstar incorporates automated
tools to set up, conduct and report
a weld inspection. With the system’s
ability to accurately size and locate
a weld defect, pipeline contractors
can
implement
engineering
methods to assess the strength
of a weld, saving potential rework
costs that could ultimately affect the
weld’s integrity. The product uses
ultrasonic technology (conventional
and phased array), as opposed to
radiography, making inspection
possible immediately following the welding process. This provides the operator
with near real-time process control.
Features include scanner mounted ultrasonics to provide immunity to
electromagnetic noise generated from welding and induction heating equipment;
modular design configured as a hybrid system with 16 conventional and 64:128
phased array channels to provide inspection flexibility and built-in redundancy;
robust packaging validated through severe shock, vibration and thermal loading
with quick-change umbilical and other mission critical components.
An advanced setup wizard allows rapid job planning, including automated
calibration block design and specification. Plus Weld data management
software seamlessly and automatically provides weld quality tracking and
trending reports for review by quality management personnel. Built in GPS
automatically tags the inspection data of each weld with its geographic location,
providing audit information to ensure every weld is properly inspected.
GE Sensing & Inspection Technologies
– USA
www.ge.com/inspectiontechnologiesGE’s Weldstar girth weld inspection
S
S
system
Infotec, with nearly thirty years’
experience gained in the field of
underground surveying and mapping,
has launched the PipeTrack mapping
tool.
Originally developed in the Netherlands
to map newly constructed HDD bores,
and designed with versatility in mind,
PipeTrack is a totally self-contained
gyroscopic mapping tool that accurately
provides 3D positional detail of virtually
any pipe, duct or culvert.
There is no requirement for surface
tracing, which means it is unaffected by
depth, material or external interference.
It can also be used in busy locations,
under housing, gardens, factories and
roads, often negating the need for traffic
management systems. The unit has
interchangeable wheel sets, enabling it
to be used with any size pipeline from
50mm diameter to the largest of man
entry structures.
Since the introduction of the new
mapping tool at the ‘No Dig Live’ event
at Stoneleigh 2006, the applications
and demand for the system have been
steadily increasing.
The accuracy of the vertical and
horizontal alignment make it is suitable
for As Laid surveys, as well as providing
the ability to identify and pinpoint belly
XYZ co-ordinates and areas of negative
gradient, whilst surveying existing
pipelines. PipeTrack also provides
health and safety benefits, especially in
the reduction of man entry surveys.
Infotec
– UK
enquiries@infotec1.net www.infotec1.netUltrasonic
inspection of large
diameter pipes with
longitudinal weld
Karl Deutsch, Germany, is a specialist
in the field of non-destructive testing.
The company’s products include
testing systems for the inspection of
longitudinally welded, large-diameter
pipes, and ultrasonic testing systems
for the inspection of ERW-welded
pipes, such as those shipped in 2004 to
Baosteel in Shanghai, China.
Non-destructive testing is an integral
part of the manufacture of large-
diameter pipes, if they are intended for
the transport of gas or oil. Karl Deutsch
produces a set of three systems for
such testing. The first system monitors
welding quality at an early stage of
production, using 18 probes.
The second testing system, with 30
probes, allows for the final inspection,
which is relevant for the user of the
pipes. The third system is responsible
for the pipe ends, which are later joined
by circumferential welds during pipeline
construction, as the pipe ends are also
safety-relevant. The test results are
recorded for each pipe and are archived
for later retrieval.
The systems are designed as a testing
portal. Such design allows for a high
throughput, with weld testing speed of
up to 1m/s. As the length of the testing
mechanics must be larger than the
pipes to be tested, the systems’ total
length is approximately 35m.
Karl Deutsch
– Germany
info@karldeutsch.de www.karldeutsch.deGyroscopic pipeline mapping tool