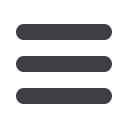

Technology News
www.read-tpt.com34
N
ovember
2013
Cutting, finishing and handling
plant installed in Saudi Arabia
ADDA Fer Meccanica has installed an
important plant for the cutting, finishing
and handling of pipes for a prestigious
tube manufacturer located in Saudi
Arabia.
The project, which took place at the
end of last year, will be used to complete
what is already present at the factory,
and AddaFer has helped to design,
construct and install a flying cut-off
double blade for pipes up to 219mm
(8"), an end facing, a hydro test and a
handling machine.
Twenty years of experience, and know-
how accumulated over many years,
have allowed AddaFer technicians to
design solutions to precise customer
specifications.
With this implementation, the Asian
manufacturer will be able to increase its
productivity and, at the same time, the
pipe quality.
The mill cut-off machine has been
optimised in order to make a near-
perfect in-line cut that is absolutely
clean and free of distortion or burr.
All functions of the unit are managed
by a microprocessor, which makes it
possible to control the machine with a
very high level of reliability, ensuring
very precise cutting lengths without
influencing the effective production
speed on the basis of which the cut-off
performance parameters are optimised.
The guaranteed bar length tolerance
is ±1.5mm at the maximum operating
speed, although significantly higher
precision is also possible.
These cut-offs are fully automatic:
once programmed they can operate
without requiring the constant presence
of the operator at the control desk; these
units are pre-tested at the factory prior
to shipment.
The base is composed of a heavy
structure in normalised welded sheet,
in which linear sliding guides are seated
in the superior side, for the support of
the cut carriage, there is a side lodging
for the rack that allows the motion of the
same carriage.
Shock absorbers and carriage block
systems are mounted at the end of
the base, for emergency, in order to
avoid damages to the rack and pinion
system.
The carriage is composed of a
normalised welded steel structure on
which all tables have been worked for
the support and the lodging of units for
the sliding of the cut heads, the vices
and the control group dimensioned for
the tracking.
The cut heads work in opposite ways
both on longitudinal and transversal
axes from the centre of the tube.
They are composed of a reduction
gear properly dimensioned with “0”
play gears which allow the rotation
of the mandrel on which the blade is
seated.
The vices are lodged in two portals
of large dimensions positioned close
to blades in order to give the maximum
stiffness to the system. They are
powered by one hydraulic cylinder.
The tracking group is manufactured
with a rack and pinion control, with
vertical axes.
Motorisation: The unit is equipped
with seven brushless motors controlled
by digital inverter of latest generation.
Functioning: In the above scheme
is shown the movement of the blades;
The profile of the tube is followed
thanks to a dedicated software (round-
square-rectangular). In this way, the
reduction of cutting time and the grades
of superficial finishing of the same tube
are evidenced.
A double vice group both at inlet and
outlet side arrange the blocking of the
tube during the phase of cut in order to
avoid dangerous vibrations.
Adda Fer Meccanica Srl
– Italy
Fax: +39 035 4946564
Email:
info@addafer.itWebsite:
www.addafer.itMilling cut-off machine with chip conveyor