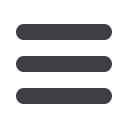

Technology News
www.read-tpt.com36
N
ovember
2013
Plastic deformation of
metal tube
IRON’S Technology, a company
located in Cesena, Italy, attended Tube
Metallurgy Russia 2013, held in Moscow
last June. The company, founded in
2011 by Rudi Bragagni, Marco Senni
and Andrea Ancarani, was there with the
purpose of submitting their invention: a
machine that allows plastic deformation
of any metal tube.
These three young entrepreneurs
started to study plastic deformation of
small diameter tubes for heat exchange
application. At the moment there is no
technology able to realise any given
shape, but it is only possible to create
small deformations by rolling.
Studies and simulations demonstrate
that increasing exchange surface and
creating turbulence inside the tube
improves heat exchange with a high
energy saving.
This necessity has given rise to the
idea of creating a machine able to
work off line tubes after production and
realising the optimal desired shape. After
four years of studies Iron’s Technology’s
engineers have settled the prototype
machine, have developed the software
and the complete new technology has
been patented.
As soon as they realised the
project the machine was thought for,
they improved the newly discovered
technology in order to obtain further and
more distorted shapes.
MAS1 (the name of the machine) is
now able to perform cold and hot plastic
deformation on tubes with diameters
ranging between 10-12 and 500mm
and thickness ranging between 2 and
8-10mm.
MAS1’s working principle is inspired
by the lathe, but unlike the lathe,
it doesn’t work by cutting but by
deformation. The machine has two tools
working in opposition on a carriage that
has a translation movement along the
axle of the tube itself.
The combination of pipe rotation and
tools translation allows deformations
able to realise a virtually infinite number
of shapes on the tube.
The technology of MAS1 makes it
possible by using tools of different kinds
and materials together with several
combination of pitch, tilt angle and
depth.
Iron’s Technology provides three size
of MAS1, depending on the size of the
tube and deformation requested: the
small, the medium and the large one,
named S, EL and HT series.
Today the company is undertaking
the second step of studying by several
cooperations with other partners in
order to find specific shapes for different
applications of tubes: internal and
external design, design and producing
of moulds, heat exchange, food,
medical, eco-innovation and motorcycle
applications.
Iron’s Technology is a start-up
company that aims to be both a machine
and tube producer, with the purpose
of developing technologies already
existing with this important innovation in
continuous improvement.
Iron’s Technology Srl
– Italy
Email:
sales.tec@ironstechnology.itWebsite:
www.irontechsrl.itFive decades of experience
STAROFIT is a major supplier for steel,
alloy steel and stainless steel butt-
welding fittings in Europe.
International orientation has always
been one of Starofit’s focuses.
The company has been actively
strengthening its international presence
and customer base. In order to better
support the growing volume and to
meet rising international demands,
Starofit has reorganised its export
departments, and formed a new team of
fittings specialists who are dedicated to
serve international customers. With the
additional flexibility contributed by this
team, the company is able to provide
rapid deliveries to customers abroad.
Starofit recently exhibited at the
Tubotech International Trade Fair in
São Paulo for a second time, and is
busy with preparations for the upcoming
Stainless Steel World Conference &
Exhibition 2013 in Maastricht, and Tube
2014 in Düsseldorf.
The company now holds in
stock seamless elbows and
fittings in material WP 304H,
dimensions ½" to 8", and has
also improved its ability to fulfil
demands for duplex stainless
steels. It stocks fittings and
elbows in material 1.4462
that are 3.2 TÜV certified in
accordance with VdTÜV 418.
Starofit has a permanent
fittings stock of 6,500 tons,
which enables it to provide prompt
responses to customers’ requests.
Its holdings range from a large stock
of ASME and EN/DIN standardised
products
to
highly
specialised
elbows and fittings with extreme wall
thicknesses and dimensions. With a
rigorous supplier selection process in
place, only products from ISO, PED
and TÜV approved manufacturers are
accepted.
The company also specialises in
demand-based tailor-made elbows
and fittings to cater to complex
requirements, and provides products
that are sustainable under extreme
conditions (eg temperature, pressure
and mediums).
Starofit Klose GmbH & Co KG
–
Germany
Fax: +49 4222 9440 44
Email:
sales@starofit.deWebsite:
www.starofit.deStarofit has a permanent
fittings stock of 6,500 tons