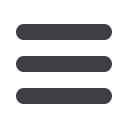

Technology News
www.read-tpt.comN
ovember
2013
71
The next Generation of Carbide Tipped
Tube Mill Saws have arrived.
Phone: 330.225.4090 • Toll Free: 800.878.8761 • Fax: 330.225.4741 • E-mail:
trucutsaw@trucutsaw.comSpecial engineered carbide tipped saw blades for orbital cutting of API
casing and Line pipe on ERW mills.
• GPX300 is the right choice for sawing API 5CT J55 to P110.
• GPX400 is the right choice for sawing API 5L tubes X42 to X100.
• GPX100 is the right choice for sawing Structural ASTM tubes.
Blades in stock for OTO MILLS, MTM, KUSAKABE, NAKATA,
LINSINGER, THERMATOOL.
Worldwide Sales • Worldwide Service.
Tru-Cut Saw
A Leading Manufacturer In Sawing Technology
www.trucutsaw.comTCSW-058_HighPerformAdTPT.indd 1
6/18/13 2:06 PM
Quick-change tube mill
T&H Lemont has shipped and
commissioned a WU35M-11 quick-
change, high frequency tube mill to a
customer currently operating other T&H
Lemont tube mills.
The mill was designed to form and
weld carbon steel and alloys up to 6"
OD x 0.312" wall standard pipe sizes,
as well as tube sizes up 6.5" OD x
0.125" wall, with material yields up to
150,000psi. For this quick mill, a second
set of sub-plates is designed to run a
heavier wall tube. This flexibility in mill
design allows the customer to serve a
number of markets, from standard pipe
to high yield tubing.
T&H Lemont designed and built
the mill with two features to decrease
change-over time and increase
productivity. The first feature was the
design and construction of the mill with
the Third Stand Quick Change System.
This system couples and connects the
mill line universal drive shafts with the
mill stand drive shafts while providing a
quick release feature when making tube
size changeovers. Each third stand is
supported and mounted to the mill base
in back of the inboard roll stand.
Quick-change third stands are
equipped with universal drive stud
supported in slide blocks which house
tapered roller bearings. Each sleeve is
assembled with a spring-loaded detent
drive pin and is connected to the mill side
universal joint bolt style flange. A drive
pin socket is supplied and mounted on
each upper and lower roll stand roll shaft
inboard input stub.
In mill run mode, each mill section
sub-plate is securely locked and held in
position by the quick change mechanical
and hydraulic cylinder system. Hydraulic
pressure maintains sub-plate position
against the rear alignment blocks and
held down by four locking bars and
posts.
During change-over the hydraulic
cylinders push the sub-plates forward
away from the stop blocks several
inches to disengage the third stand
adapter sleeves. Once clear of sleeve
engagement, an overhead crane is
attached to the sub-plate to vertically lift
and remove the sub-plate from the mill.
The new sub-plates are positioned
and placed over the mill base locking
posts. The hydraulic cylinders are then
used to pull the sub-plates back against
the mill base stop blocks and are locked
in run position.
While the sub-plates are being pulled
back, the adapter sleeve spring loaded
detent drive pins depress. Once the
sub-plates are hydraulically secured,
the mill drive is jogged and all of the
spring-loaded detent pins align with the
inboard drive pin socket slots, and snap
into place. After final set-up checks, the
mill is ready to run.
Air cylinders and stop blocks will be
utilised to locate the upper and lower roll
shaft position of the third stand to match
the inboard stand. With this feature the
set of sub-plates can be set up off-line.
The second feature designed for this
mill is the AutoSet System, for precise,
automated roll adjustment. The system
is designed to minimise set-up times.
Using encoder and drive technology,
the time required for roll adjustment on
a new set-up is reduced and can be
accomplished from the operator station
without the use of hand tools.
Utilising AC vector drives, a PLC,
absolute position encoders and a
colour touch-screen interface, the mill
can be programmed to have the rolls
automatically return to a predetermined
location.
In addition to complete production
systems, T&H Lemont provides a variety
of components and services to the
tube, pipe and roll-forming industries.
Services include tube and pipe roll
design, mill alignment and operational
consulting. Components offered include
cut-offs, entry equipment, accumulators,
seam orientation stands, weld boxes,
edge conditioners, bead scarfing
systems, straightening systems, single
point adjustment systems, dedimplers,
rolls, blades, jaws and shafts.
T&H Lemont
– USA
Fax: +1 708 482 1801
Email:
sales@thlemont.comWebsite:
www.thlemont.com