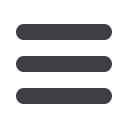

Technology News
www.read-tpt.com74
N
ovember
2013
Speed and precision
for tube forming
transfluid
Maschinenbau
GmbH,
Germany, designs individual solutions
for tube processing which guarantee
excellent production times and value for
money for the customer.
transfluid designs advanced tech-
nology which copes with the special
challenges of tube forming intelligently.
Tube endforming machines for the
axial use – with supplementary clamps
and up to eight stages as well as
horizontal and vertical tool change –
are available as well as rotary forming
machines which can form tubes with
the rotation procedure, and roll beading
machines (from 4 to 168mm) which
can be used in versatile ways to form
geometries from outside to inside, from
inside to outside and to cut the tube.
To reach ideal tube results it is
important to complement the tube
forming to the tube bending process or
to use it as a stand-alone process. REb
is the series of forming machines for
extreme degrees of tube forming, rapid
tool changes and complex geometries –
allowed by the supplementary clamping
unit. These systems are suitable for an
economical mass production process at
the highest level.
To give already axially formed tubes a
further form and to produce an excellent
surface and sharp-edged contours for
sealing elements, the solution provider
transfluid designed rotary and CNC-
controlled tube forming machines,
which enable an optimised production.
Customers can find it in the series SRM
in the t form portfolio.
transfluid can be visited at FAbTECH
Chicago at stand S5684.
transfluid Maschinenbau GmbH
–
Germany
Website:
www.tube-processing-machines.comSpent
emulsions
SEPAR 5000, installed in the
Marcegaglia Industries headquarters in
Gazoldo degli Ippoliti, Italy, has a broad
versatility. It is claimed to be the largest
ultrafiltration plant ever built in Europe
for this kind of application, with a normal
treatment capacity of 8,000l of spent
emulsion and 1,000mc of recirculating
emulsion per hour.
The unit can treat a broad range of
emulsions: mineral oil-based emulsion
(eg from rolling mill and tube profiling);
synthetic lubricoolant (eg from tube
profiling or from skinpass of coils);
solvent-based lubricoolant (eg from tube
cleaning or from stainless steel skinpass);
spent alkaline degreasers; and water and
oil mix (coming from pit cleaning).
Condoroil
– Italy
Fax: +39 0332 945303
Email:
info@condoroil.itWebsite:
www.condoroil.it