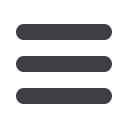

88
N
ovember
2013
2013
V304 plasma and oxy-fuel
cutting system
DURING Fabtech in Chicago, Voortman
will show for the first time the Voortman
V304 plate processing system on booth
S1773. The V304 with multi-torch oxy-
fuel cutting, plasma straight cutting
and plasma bevelling will be officially
revealed to the public. Also the V320
combined plate cutting and drilling
system as well as the V630 beam drilling
system will be demonstrated.
The V304 is one of the successors
of the VCS Compact, VCS Thermo
and VCS Multi from the VCS range
of plate processing systems. It has a
maximum working width of 13 feet and
a table length of up to 80 feet. The V304
can process material up to 8" thick.
The V304 can be equipped with two
plasma torches, six oxy-fuel torches or
a combination of all which makes this
system suitable for large production
runs and repetitive pieces.
The V304 is one of the new
developments in the Voortman plate
processing range and has the following
new features:
The V304 can be equipped with up to
six oxy-fuel torches to achieve a higher
output or to cut strips from stock plate
simultaneously. The automatic ignition
eliminates any manual intervention and
thus saves valuable time. The automatic
gas supply always provides the cutting
torches with the right amount of gas.
The oxy-fuel triple torch module was
developed for weld preparations and
produces X, Y, K or V cuts to simplify
further production steps.
The V304 can be supplied with a large
variety of plasma sources for different
cutting processes and different material
thicknesses.
A maximum of two plasma torches
can be mounted to the machine for
simultaneous cutting plates up to
3.2" with the HPR 400XD or thicker
depending on the plasma source.
An automatic 3D bevel unit makes it
possible to produce X, Y, K or V cuts for
weld preparations up to a bevel angle of
50°.
Available on the V304 is True Hole
Technology from Hypertherm
®
and
Contour Cut from Kjellberg
®
to create
exceptional hole qualities compared to
the conventional cutting methods. An
automatic gas control switches from
cutting to marking if required
and ensures the right gas
combination and gas flow during
the entire cutting process.
The V304 is equipped
with high precision gantry
movement by means of double
synchronous driven servo drives
in combination with double
linear guides and helical rack
and pinion system. The linear
guides are covered to eliminate
contamination and extend the
working life.
Nesting software: Voortman
offers various nesting programs
on the V304 from simple nesting
software to advanced optimising
software for saving valuable time
and material.
Voortman
– The Netherlands
Website:
www.voortman.netPipe manufacturing equipment
NAKATA Manufacturing, a provider
of support of pipe manufacturing
equipment from design to follow-up
services, has been developing the next
generation of its pipe-making machine:
the FF3rd, also known as ODF.
ODF makes use of multiple die blocks,
which are connected together and move
in the circumferential direction on an
endless track. Due to the continuous
constraint on the edge of the strip, both
heavy gauge and extra-thin pipes can
be formed stably without any slippage
between tool surface and forming
materials.
With a compact configuration of
mill line, there is no need to change
any forming die before fin-pass at the
maximum OD range 3:1, with less
forming strain than roll forming and
higher productivity.
Nakata Mfg, Co, Ltd
– Japan
Fax: +81 6 6303 1905
Email:
sales@nakata-mfg.comWebsite:
www.nakata-mfg.com