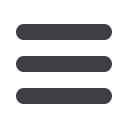

92
N
ovember
2013
2013
Medium and large diameter fully
electric bending machines
FOR many years the market has been
requesting Crippa to supply machinery
and solutions in the field of large-
sized tubes (between 100 and 150mm
diameter).
However, despite having several
projects in the drawer that have been
kept in continuous progress and updated
at the pace of technology progress
and daily experience in the field, the
company has always preferred to focus
its offering on lower sized machinery in
diameters up to 80mm.
After completing the “full electric”
offering in diameters up to 80mm, Crippa
has entered into the large diameter
field with an innovative fully electric
machinery platform, which uses the
entire experience from Crippa that was
acquired across over 60 years of activity,
and meets customers’ needs and
market trends. The mission is to reaffirm
the Crippa role as the preeminent
field reference in large diameter tube
manipulation.
The fully electric offering for large
diameters was developed through
machinery that is built based on
specific objectives and issues, such as
conceptual and operating simplicity, full
structural rigidity, flexibility, sustainability
considered
as
energy
saving,
ergonomics, ecology, and using state-
of-the-art technology, and characterised
by the greatest operating flexibility and
the widest possibility of customisation,
tailor made according to users’ needs.
There are two new models of these
bending machines, the CA N114 and
the CA N150.
Some main characteristics and
functions
include:
tube-bending
machines for tubes to 114 and 150mm
diameter; the concept of these
bending machines is to reach the
utmost structural rigidity on several
tube-bending planes, combined with
construction simplicity and the use,
where possible, of direct control
transmission.
Wide use of digital “full electric”
axes, being activated and controlled
by servo motors and Siemens CNC,
which compared with hydraulic
machinery, ensures higher precision,
repetitiveness
and
ecological
characteristics such as energy saving,
silence and cleanliness; the use of
state-of-the-art
electronic
devices
ensures the minimising of the electrical
power used during manufacturing with
a considerable economic
saving over time.
The time schedules for
changing tooling and pro-
gramming are minimised
as no mechanical adjust-
ments are required.
The roller bearing
guides for mounting and
scrolling of equipment
promote the precise posi-
tioning and controllability
of all axes.
Existing tooling sets
owned by customers
may be used, thanks to
the high vertical Z-axis
excursion and particular
mechanical solutions, eg
the customisable die holder flange in the
area where the equipment is mounted.
The one-block bend arm is built by
building in the clamp-blocking axle with
the benefit of rigidity and precision, as
well as the possibility of bending tubes
with very small pipe radius; knife-shaped
tube cutting device which can be built
on the machines for sequential cutting
operations in the same manufacturing
cycle.
With dramatic reductions in process
scrap achievable; possibility of
integrating the machinery with “tangent
boost”, a device that limits the swerve
on the last curve of any bent tube, with
considerable material saving.
Bending machines that can be
fully programmable with the use of
the graphic interfacing Software “UII”
developed by Crippa, which ensures
the possibility of carrying out accurate
feasibility analysis and accurately
simulating the bending; thus ensuring a
fast manufacturing stage and successful
manufacturing from the first sampling.
The fine-tuning of program steps can
be achieved by optimising the program
generated by a graphic simulator through
ISO code processing; the number of
working planes is variable according to
the geometry of the tube to be bent and
any different bending radii; guarantee of
bending with a very high diameter/width
ratio and a very small bending radius;
possibility of bending with variable
radius; ease of tube loading and
unloading either in manual or automatic
mode, thanks to a very ergonomic
loading area; right or left bending sense;
and high repeatability and precision
but also reliability thanks to the use of
electrical/electronic components and
devices, which are currently some of the
best on the market.
The new technology is suitable for
many applications, especially for those
who operate in automotive (lorries and
earth movement), railway, aviation and
plant design and for people who have
to face hard bends on large diameter
tubes, narrow and often small bending
radius.
Crippa
– Italy
Email:
carlo.fratini@crippa.itWebsite:
www.crippa.itBending of up to 150mm can now be undertaken
An example of a Crippa bend