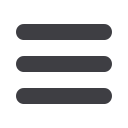

T UBE M I L L S & R OL L FORM I NG L I NE S
www.read-tpt.comMAY 2017
67
Cross section scanning for tube makers
MOST optical profile measuring systems
are in-line devices equipped with a
sensor ring with four to six cameras.
This can make quality control a costly
and inflexible obligation, as camera/
laser modules represent the most
expensive parts of an optical
measurement system. Additionally,
sensor ring-based devices lack
flexibility regarding the range of
views.
The Copra
®
ProfileScan Desktop
with patented 360° measuring
method addresses both of these
problems, using only one sensor
module and a turntable.
In addition to high accuracy,
Copra ProfilScan Desktop offers
flexibility and mobility due to
the compact build. It is quickly
assembled and can be deployed
in other production locations using
the provided transport case. With its
high range of views and full integration
into the Copra workflow, ProfileScan
Desktop is also suitable as a measuring
tool for reverse engineering projects.
Paired with the provided software
solutions, Copra ProfileScan Desktop
can be applied in various ways by tube
makers. Designers can measure cross
sections of roll-formed round tubes
after each station and therefore both
evaluate the manufacturing quality
and locate deviations at different
production sites. These features
also make the device suitable
for measuring shaped tubes with
different radii.
Copra workflow integration allows
the designed contour from Copra
RF to be compared quickly, and
visualised in the form of a deviation
diagram.
data M Sheet Metal Solutions
GmbH
– Germany
Fax: +49 8024 640 300
Email:
datam@datam.deWebsite:
www.datam.deCopra ProfileScan
Desktop 80
Tube mills for precision tubes
made of high-strength steel
CELEBRATING over 40 years in the
business, Officine MTM SpA designs
and manufactures tube mills, as well as
related equipment and tooling dedicated
to the production of precision tubes and
welded profiles. Following the market
trend, the company is presenting its
range of machinery designed to produce
precision tubing from high-strength
material.
The requirement to provide increased
safety in the automotive and other
industries by limiting weight and using
thinner sections has led to the use of
high-yield materials (100,000 psi and
above), challenging tube manufacturers
to the limits of current forming and
welding technology. Through extensive
R&D and practical experience, Officine
MTM can offer solutions. The fully
automatic entry line allows enhanced
productivity and ensures the standards
of quality and material identification
required by the automotive industry.
The company states that the strong
design, the use of high-quality material
and components, and the precision of
workmanship result in a highly stable
mill platform capable of handling high-
yield materials and extreme diameter
to wall ratios (eg WT/OD below 1:7 or
above 1:80).
Officine MTM is also highlighting its
high-performance flying cut-off and
saw units, in addition to its single and
double cold saw units designed for high
performance and speed.
The M&K 3.5 dimple-free flying
cut-off can process square and
rectangular profiles in stainless steel up
to 4mm thick at a maximum speed of
180m/min.
The requirements of short-length
profiles in high-strength material with
high quality of cut and high speed of
production are met by the features of the
M&K 3.5 cut-off.
Officine MTM SpA
– Italy
Fax: +39 041 999611
Email:
sales@mtmtubemills.comWebsite:
www.mtmtubemills.comThe M&K 3.5 dimple-free flying cut-off