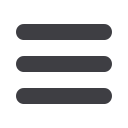

T UBE M I L L S & R OL L FORM I NG L I NE S
www.read-tpt.com72
MAY 2017
Rafter ships RT-3000 weld box and
turkshead for profiles
RAFTER Equipment Corporation has
delivered welding and straightening
equipment to a major North American
custom roll form parts producer. The
equipment included an RT-3000 high-
frequency induction (HFI) five-roll weld
squeeze box and an RT-3000 double-
sided turkshead straightener. The equip-
ment will be used for the production of
HSLA welded seam profiles up to 3"
square x 0.16" thick for an automotive
application on the customer’s existing
RLM Manufacturing roll former. Rafter
states that it was chosen for the project
because of its reputation for providing
the kind of heavy-duty mill equipment
necessary for this application. Rafter
is a manufacturer of tube mills, pipe
mills, roll forming machines, cut-off
machines and other related tube and
pipe mill machinery. Additional services
include rebuilding and upgrading mill
equipment.
Rafter Equipment Corp
– USA
Fax: +1 440 572 3703
Website:
www.rafterequipment.com50 years of roll-forming exper tise
SEN Fung is a supplier of sheet metal
roll-forming machinery in Taiwan, and
has operated in the roll-forming industry
since 1963.
Withmore than 50 years of experience,
the company offers quality, durable and
customer-orientated facilities worldwide.
Sen Fung is also able to manufacture
high-speed and automated machinery.
Numerous inventions are patented in
different countries. The company says
that its service team is qualified and
praised for its accurate and quick after-
sale service reputation. Sen Fung offers
technical and machine support to meet
the needs of its customers.
Sen Fung Rollform Machinery Corp
– Taiwan
Email:
service@senfung.comWebsite:
www.senfung.comSen Fung has worked in roll-forming since 1963
Gasparini presents the X-Press
SHEET metal is labelled according to
its minimum yield strength. A36 steel
corresponds to 36,000psi but will
include much stronger steels. Rolling,
holes and cuts create internal stresses,
which means that sheet metal can be
unpredictable.
During forming, upper ram bows in
the centre. There, the punch will be
farther from the die, so the angle will
be sharper at the ends and wider in the
middle. A difference as small as 0.0019"
in depth leads to a 1° difference on a
0.3" V-die.
This effect is corrected by crowning:
the table is raised to keep the die at a
constant distance. But how much do we
have to raise? Most manufacturers rely
upon theoretical plate strength charts.
This is often pointless because the
material is unpredictable.
To solve this issue Gasparini has
patented the ACSG active crowning.
A sensor in the ram detects bowing.
Cylinders in the table raise the die,
while another sensor measures the
height. When the two values are equal,
punch and die are at the same distance
and the profile will have a constant
angle across its length. ACSG is just
one of many accessories that make
X-Press one of the most advanced
press brakes available.
X-Press is a tailor-made machine
entirely designed and built by
Gasparini, including the frame and the
hydraulic circuit. More than 40 years’
experience led the company to develop
many exclusive custom solutions.
Gasparini
– Italy
Website:
www.gasparini.it/en