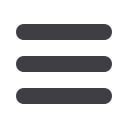

ROUND UP
Excellence in refurbishment of critical electrical rotating machinery
A recent project undertaken by
Marthinus-
en & Coutts
, a division of ACTOM, was the
rewind and refurbishment of three gearless
mill drive rotor poles for a platinum mine
in the NorthWest Province.The enormous
17,5 MW 4 220 V 2 531 A 12 r/min 5,8 Hz
grinding mill motors, that are 15 metres
in diameter, are driven by cycloconverters
which supply the motors with a variable
frequency to control their torque and also
allow the speed to be controlled for opti-
mum metallurgical processing.
Rob Melaia, engineering and technical
executive at Marthinusen & Coutts, said:
“The rotor poles were subjected to over-
heating due to an operational error, and
we were approached by the mine to assist,”
Melaia says. “While this contract could be
seen as a simple procedure, we believe it
is the immediate access to a large local
service provider with OEM capabilities and
back-up that led the customer to award the
contract toMarthinusen & Coutts instead of
to the international OEM.”
The removal of the poles required a
two day shutdown during which time
Marthinusen & Coutts assisted the mine
maintenance personnel with this task.The
poles were delivered to Marthinusen &
Coutts’ Cleveland facility where thorough
investigative work was undertaken on the
defective poles to determine the extent of
the damage caused by the overheating.
“The second part of this activity was to
investigate the best method to improve
and partially rectify the surface insulation
of the remaining poles of which there are
60 in total,” adds David Motloung, design
engineer at Marthinusen & Coutts.
Marthinusen & Coutts made use of a two
part epoxy spray treatment and repeated
insulation resistance tests under extremely
wet coil conditions.
David Motloung said that this was to
simulate the worst case conditions on site
with the ultimate purpose of evaluating a
method devised by Marthinusen & Coutts
to improve the insulation of the remaining
poles still fitted to the machine. “This solu-
tion can be implemented in-situ negating
the need to remove the poles to improve
the insulation,” he explains.
Motloung says that after studying the
design of the pole coil it was decided to
use a different conductor for the rewind as
this would increase the insulation integrity.
Enquiries: Richard Botton.
Tel. +27 (0) 11 607 1700 or
Local company powers Mozambican graphite mine
The remote operation to mine one of the world’s largest finds of
high grade graphite – the Balama deposit in Mozambique – will be
powered by a generator plant being constructed through South
Africa-based Zest Energy, part of the
ZestWEG Group
.
According toAlastair Gerrard, managing director of Zest Energy,
the plant will begin producing electricity during the first quarter
of 2017, with an initial capacity of 12,5 MW from an installation of
seven 2 200 kW diesel generators.
“The isolated location of the Balama mine – over 250 kmwest of
Pemba in northern Mozambique – means that while the operation
does have access to power from the national
grid this will need to be supplemented to ensure
an adequate supply for full plant demand,” Ger-
rard says. “We are therefore required by the
customer to ensure 100% availability, and have
consequently designed the plant with substantial
standby capacity to allow for maintenance and
repairs without affecting the continuous supply.”
He says the plant, which was the largest foot-
print project yet tackled by Zest Energy, would
initially run with seven 2 200 kW generators; six
running and one on standby, and would later be
expanded to include eleven generators, of which
two will be standby units. Equipment for the ex-
tensive scope of supply has been sourced from
various companies within the ZestWEG Group, locally and world-
wide.The containerised power generators includeWEG alternators
with automatic voltage regulation systems, as well as motorised
louvres, generator auxiliary systems, and fuel and lube tanks.
To cool the engines, a horizontal-type radiator system, rated for
50°C ambient temperature, was manufactured in South Africa and
each radiator includes 10 WEG 3 W fan motors positioned in two
cooling banks of five fans each.
Enquiries: Kirsten Larkan.Tel. +27 (0) 11 723 6000 or email
marketing@zestweg.comDRIVES, MOTORS + SWITCHGEAR
Marthinusen & Coutts' rotating machines design engineer, David Motloung,
records photographic evidence of tests on one of the enormous gearless mill
drive rotor poles recently refurbished by the company.
Electricity+Control
January ‘17
16