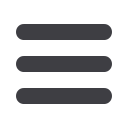

N
ovember
2008
www.read-tpt.com24
›
T
echnology
U
pdate
CNC bending directly from CAD to bender
Winton Machine, USA, has introduced its newest rotary draw-bending machine. The
RD30eCNC is an economical and easy-to-use 3-axis CNC rotary draw bender.
This PLC driven machine offers an
optional PC interface that enables the
user to import a STEP file right from
CAD directly to the bender without
typing in a single data point. This
capability not only saves time but also
cuts down on programming errors.
Winton’s eCNC line of mandrel
benders is suitable for job-shops
and OEMs, providing an increase
in productivity, reduced cycle time,
and improved quality. The series
consists of 20mm, 30mm, and 50mm
machines with a tubing range from
1mm OD to 50mm OD.
An optional PC interface allows for programming and data storage.
Winton Machine Company
– USA
Fax
: +1 770 831 6459
:
gwinton@wintonmachine.com•
Website
:
www.wintonmachine.com
The RD30eCNC 3 axis CNC rotary draw bender
Online process analysers
for automated high volume quality control
(up to 300 more) using a simple, one-
minute procedure. Once the unit has been
taught a fingerprint, it will not need periodic
recalibration.
Positive material identification (PMI) quickly
identifies an alloy in seconds by matching
the spectral signature of the unknown
sample to spectral signatures of reference
standards stored in the library.
The chemistry of the alloy is then calculated
using stored elemental assays, with the
identified grade as reference standard.
Specific materials can be simply and quickly
added to the library.
Analytical mode utilises a fundamental
parameters (FP) algorithm to determine
elemental chemistry. The FP calibration is
done at the factory, and requires no user
setup or recalibration. The FP method used
in analytical mode is suitable for applications
that require analysis of proprietary or
uncommon alloys, monitoring chemistry
of tramp elements, and a monitoring
chemistry during processing. The analytical
mode can identify an unknown material in
approximately 5 seconds, with increased
precision for longer test times.
The Innov-X Fox-IQ system consists of
three major industry hardened components.
The probe head assembly (PHA) contains
the x-ray tube, detector, and front-end
digital signal processing electronics. The
PHA can be pre-calibrated, and its modular
design allows exchange in minutes.
The electrical interface assembly supports
an external sample trigger input, and
provides a pass/fail indicator signal that
can be used to trigger a ‘kicker’ or other line
equipment like PLCs to accept or reject the
sample, based on the analysis result. The
user interface computer runs Innov-X PC
Tube and pipe manufacturers use many
different metals and alloys in production
lines. To eliminate liabilities, avoid material
mix-ups and meet customer requirements,
they must compare products against
acceptable alloy specifications.
Particularly in the aerospace, petrochemical,
nuclear and other demanding industries,
the consequences of processing or
fabricating with the wrong alloy material can
be catastrophic, resulting in product failure,
personal injuries, fatalities, liability claims
and eventual loss of business. To protect
their business, high volume manufacturers
need a fast, non-destructive method that
checks each piece prior to shipping.
Fox-IQ online tube analysers from Innov-X
Systems offer these capabilities in an easy
to use and reliable solution. The compact
system integrates easily with existing or
new processes, and provides continuous
online measurements to optimise processes
for increased productivity and improved
product quality.
The systems perform fully automated online
analysis for 100 per cent high-volume
process control. X-ray fluorescence (XRF)
is a proven analytical technique commonly
used to quickly and non-
destructively perform multi-
element analysis on solids,
liquids and slurries – for
example to verify alloy grade
and chemistry.
The rugged process analysers
are designed and engineered
for 24/7 operation in the
harsh industrial environment
of manufacturing plants. They
can endure high levels of
vibration, electromagnetic and
acoustical noise. They offer a
combination of speed, accuracy and cost
effectiveness, with worldwide service.
Long-term service contracts are available
to assure high levels of system up-time.
The Fox-IQ systems have several modes
of operation. Pass/fail mode is designed
for high-throughput alloy sorting and quality
control. All sorting is done by comparing a
sample to an operator-selected reference
fingerprint. The system will provide a pass
or fail result in just a few seconds.
The system comes with a standard
reference library of common alloy
fingerprints, and users can add their own
The Fox-IQ online tube analyser features a compact design,
allowing it to be integrated into most existing operations