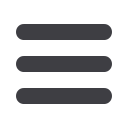

25
N
ovember
2008
www.read-tpt.comT
echnology
U
pdate
›
Expert in tube mills upgrades finite element analysis system
Roll-Kraft, USA, has upgraded its system for finite element analysis, in response to
increased demand for such services from both the rollforming and tubing industries. The
update includes the integration of a new, high-performance, dual-processor computer.
Upgrading the Copra RF FEA software from Data M Software is designed to take
advantage of the new computing power.
The new release of the FEA software has increased functionality. An engineer can
designate which roll passes are driven and non-driven, as well as define the line
speed and account for friction in the tooling. The program is also able to simulate non-
symmetrical, formed-up welded profiles.
Early tests have resulted in a calculation time reduction of approximately 75 per cent,
compared to the previous FEA system. The increased capacity will allow Roll-Kraft to
use the FEA more effectively during the design phase of the project.
The improvements in both speed and functionality will benefit customers in several
ways. The decrease in calculation time will permit the running of more simulations of
various tooling design concepts during the engineering phase, in order to develop the
best possible solution for producing an accurate profile. This will, in turn, decrease the
amount of time a set of tooling spends in the testing phase. The addition of the rotating
rolls, line speed, and friction functions will better allow the prediction of possible surface
condition problems in the finished product.
With many industries switching to lighter, stronger materials and more complex profiles,
the need for a scientific approach to tooling design has become necessary. Roll-Kraft
often uses the FEA system in an R&D role, and collaborates with existing and potential
customers to determine the feasibility of rollforming these advanced materials and
products.
Roll-Kraft
– USA
Fax
: +1 440 205 3110 •
Website
:
www.roll-kraft.comInnovative inline bright annealing system
Elind SpA, Italy, is the manufacturer of
complete solutions for induction heating
applications. These applications include
rolling mill operations, hot forging, and
heat treatment such as hardening,
tempering, annealing and heating of tube
and pipe.
Following its experience in the field of
stainless steel tube annealing, Elind has
developed an innovative inline bright
annealing system for work on TIG and
laser welding stainless steel tube mills.
The equipment is composed of three main
sections: heating, soaking (available on
request) and cooling.
The concept of modularity is applied on all
three sections of the equipment that can be
tailored to the needs of the end-user and
easily improved in field in terms of number
of inductors, power and cooling section
length. The heating and soaking sections
are composed of one or more inductors
driven by a generator with an output power
ranging from 50-500KW.
The generator is based on a high efficiency
IGBT inverter of the latest generation,
which is able to work within a wide range
of working frequencies. The cooling section
has been designed for achieving the
best results in terms of short cooling time
and to make fast and easy the change of
tooling. Both inductors and cooling section
are assembled onto a movable water-
cooled frame that can easily be removed
from the tube mill in case annealing is not
required.
Stainless steel tube is heated up to the
annealing temperature (which is main-
tained for a while if
the soaking section
is
used),
and
subsequently cooled
down. The entire
process is performed
in a pure hydrogen
atmosphere
for
keeping the surface
of the tube clean and
bright.
The equipment is extremely safe due to
special seals fitted at the input and output
areas, together with a sophisticated gas
management system.
A temperature control system ensures a
constant annealing temperature even in
cases of possible feed variations of the mill.
The standard equipment is supplied
complete with a separated cooling unit and
an operator control panel.
Elind SpA
– Italy
Fax
: +39 011 95 72 502
:
info@elind.netIndirizzo
Website
:
www.elind.netsoftware to control the instrument, analyse
samples, manage results and interface
with external devices through RS 485 or
TCP/IP.
The system includes automatic operation so
no operator intervention is required, while a
robust industry hardened design requires
minimal maintenance. It is possible to
monitor up to 25 elements simultaneously
from P to U – from ppm to high percentage
levels. Other features include remote
diagnostics, integrated standardisation for
automatic analyser QC and performance
verification, and minimal downtime, as pre-
calibrated probe head assemblies can be
exchanged in minutes.
The compact design will fit into most existing
operations with minimal infrastructure
changes. The system has low power
requirements, needing only 110/220V, and
uses a low cost, low power x-ray tube,
eliminating the regulatory headaches of a
radioactive source.
Innov-X Systems also supplies portable and
handheld alloy analysers for pass/fail and
PMI verification.
Innov-X Systems
– USA
Fax
: +1 781 938 0128
:
foxiq@innovx.comWebsite
:
www.innovx.com
Elind offer a new inline bright annealing system