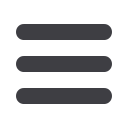

29
N
ovember
2008
www.read-tpt.comT
echnology
U
pdate
›
Instrumented DTW testers readily provide
this type of data, and crack propagation
energy can be directly derived from test
results. As an aside, work done by Pohang
University in South Korea has demonstrated
that while Charpy USE has a very weak
correlation with DWTT propagation energy,
it has a very strong correlation with DWTT
initiation energy, supporting the hypothesis
that for high strength steels almost all the
energy in a Charpy test goes into initiating
the crack.
The breakdown in the usefulness of Charpy
USE as a predictor of fracture toughness
has led investigators, since the 1980s, to
look towards more theoretical approaches
based on fracture mechanics variables.
These variables include crack-tip stress or
strain, crack-tip opening displacement or
crack-tip opening angle (CTOA), and crack-
tip force or energy release rate. Important
work at the Centro Sviluppo Materiali in
Rome, amongst other institutions, has
concluded that the most appropriate
variable for modelling stable crack growth
is the CTOA at a specified distance from a
crack tip, or CTOAsc.
There are a number of ways of measuring
CTOA, one of which is direct measurement
using a high-speed video camera.
A well known indirect method is the
two-specimen CTOA test or TSCT.
This uses absorbed energy values for
multiple DWTT-like specimens with
different notch depths to derive the
CTOA value.
Work at Pohang University in South
Korea and others has shown a strong
correlation between CTOA and DWTT
propagation energy (specifically, a linear
relationship between the propagation
energy and sin[2 CTOAsc]). Although more
work needs to be done to validate this
relationship for a range of materials and
specimens, this work suggests that it is
possible to make a measurement of CTOA,
an important material parameter, using a
single specimen in an instrumented DWT
tester.
Of course, instrumenting a DWT tester is not
a trivial matter: the forces that are generated
when impacting high strength steel samples
with thicknesses up to 50mm can exceed
1 MegaNewton: not only do these forces
have to be measured accurately at high
bandwidth, but the compliance of the
apparatus needs to be low enough to make
these measurements meaningful.
The drop weight has to be precisely
guided to ensure that the hammer is kept
perpendicular to the plane of the impact.
Considering that on higher capacity
machines the total impact energy is
100,000J or more, and over its lifetime the
apparatus must endure tens of thousands
of such impacts, the design represents
a challenging combination of heavy
engineering and precision.
This article was supplied by Nick Osborne, technical
director of Imatek Ltd
Imatek Ltd
– UK
Fax
: +44 1438 829054
:
info@imatek.co.ukWebsite
:
www.imatek.co.uk
DWTT results