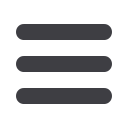

N
ovember
2008
www.read-tpt.com32
T
echnology
U
pdate
›
undertaken by means of the bent inductor
and the associated medium-frequency
infeed unit. This method is suitable for an
array of materials.
After forming, the wall thicknesses are
nearly identical over the complete pipe.
In addition, the cross-section of the pipe
bend maintains the circular contour of the
starting pipe.
SMS Elotherm GmbH
– Germany
Fax
: +49 2191 891 726
:
m.oelmann@sms-elotherm.deWebsite
:
www.sms-elotherm.comand be connected to the
PLC via Profibus facilities.
Two temperature cameras
installed at the inductor
outlets provide the data for
power setting as a function of
the pipe feed motion.
The
Hamburg
method
for the production of pipe
bends involves pushing pipe
sections over a mandrel
which has the curvature
required for the finished
pipe bend. The feed-forward movement
is accomplished by means of a hydraulic
press. The pipe is heated in two zones.
Preheating is accomplished in the straight
part of the inductor without any material
deformation or forming, while the bent
inductor serves to heat the pipe to the
desired final temperature. It is here that
forming takes place.
Heated to final temperature, the pipe is
pushed over the mandrel by the press,
and thus takes the shape of the mandrel.
This method requires the mandrel to be
heated before production starts, which is
SMS Elotherm, Germany, has received an
order from Tectubi Raccordi SpA (Allied
Group), an Italian producer of pipe bends,
for a ‘Hamburg method’ inductive heating
plant for the production of pipe bends.
With inductor power inputs of 2,400kW
and 1,600kW, the plant is claimed to be
the world’s most powerful of its type.
Commissioning is scheduled to start at the
start of 2009.
The scope of the order includes the
equipment for preheating the still straight
pipe section, plus two medium-frequency
infeed units for heating the bent pipe
section. In addition, the order covers three
sets of inductors for the production of pipe
bends with diameters from 36" to 56".
The heating plant will be designed for bends
of standard steel and austenitic grades,
and will be able to process pipes with wall
thicknesses of up to 60mm. The power input
of the first inductor amounts to 2,400kW,
while the bent inductor will be rated for a
maximum power input of 1,600kW.
The transistorised converters will be
equipped with SMS Elotherm digital control,
Inductive heating plant for 56" Ø pipe bends
Fabrication of a 24" pipe bend with inductive heating