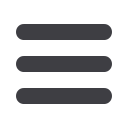

37
N
ovember
2008
www.read-tpt.comT
echnology
U
pdate
›
The power station reported increased output
accompanied by cost savings through
lower fuel consumption. American Electric
Power (AEP) was able to report lower CO
2
emissions through less fuel being burnt.
Checks on the tube walls revealed that
none needed replacement, and the cleaning
and inspection operation was successfully
completed within agreed time scales.
Tube Tech International Ltd
– UK
Fax
: +44 1268 786998
:
webinfo@tubetech.comWebsite
:
www.tubetech.comtheir way. This was followed by eddy current
inspection, in which an electromagnetic
probe measured tube-wall thicknesses and
highlighted any excessive wear.
The benefits of the Conco bullet system
include uniform cleaning of each tube
and a high level of safety, as no high-
pressure water is used. The system cleans
effectively, resulting in extended tube life
through improved surface conditions. Tubes
cleaned with this method are claimed to
have a better vacuum and an improved
heat transfer rate.
features including multi-channels, multi-
frequencies, frequency range from 10Hz to
10MHz, a supervision system which allows
control of all peripheral devices, sorting
management and reporting.
Reports provide information on defect
location, type, number of good and bad
parts and different rates, with a virtually
unlimited number of parameter sets.
Remote control via the internet offers the
possibility of supervision or support from
anywhere in the world.
The
Zet@premiumand the
Zet@Microcomplete the range, providing flaw
detection, material sorting, hardness or
surface treatment inspection. A complete
range of accessories is also available.
Controle Mesure Systemes
– France
Fax
: +33 3 85 94 14 15
:
contactcms@cmseddyscan.comWebsite
:
www.cmseddyscan.comBullet cleaning system
for condenser tubes
Tube Tech International Ltd, UK, has
employed technically-advanced methods
to achieve high standards of condenser
cleanliness at the Fiddler’s Ferry Power
Station, near Warrington, UK.
The company’s contract for the operation at
the power station gave it a dual role – the
cleaning of two condensers and inspection
of one.
Two of the main condensers at the power
station were operating at reduced efficiency
as a result of deposits on the inside of the
tubes. Cleaning is a huge task in itself as
there are a total of 81,480 tubes (40,740 in
each condenser).
An additional function for Tube Tech
technicians was to check the tube-wall
thickness of one condenser and to establish
if any required replacement or plugging.
It was vital that downtime be kept to a
minimum, as the turbines were undergoing
overhaul and the condenser cleaning
operation was being carried out at the same
time as other work.
Tube Tech employed a combination of
a new Conco condenser bullet cleaning
system and Tube Tech’s own Rotaflex. In
this operation, metal scraper bullets are
propelled down the tubes using high volume
water, removing the offending deposits on