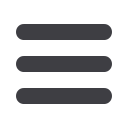

N
ovember
2008
www.read-tpt.com42
T
echnology
U
pdate
›
components and so CNES also had to cope
with a mixture of original imperial drawings
and new metric ones to build the machine.
”
Corus Northern Engineering Services
– UK
Fax
: +44 1642 404726
:
cnes@corusgroup.comWebsite
:
www.corusnes.comThese products include gas turbine engine
shafts, structural and landing gear forgings
for military and civil aircraft, as well as
manifolds, sphere tees, valve bodies and
seamless pipes for the offshore oil and
gas industries. The new machine is part of
a significant capital investment expansion
project at the company’s Livingston site.
The plant boasts one of the world’s largest
‘clam shell’ furnaces, which is used to heat
treat the seamless pipes.
The CNES machining workshops in
Scunthorpe are equipped with heavy duty
cranes, lifting gear and machining facilities
required to carry out the new grinding
machine build. The majority of the new
machine (in terms of weight) is in the rails
and travelling beam, which had to be lifted
in one piece, and so heavy duty lifting gear
was required.
John Backhouse, business development
manager, offshore and energy at CNES
said, “
Our engineers had to manufacture
the new grinding machine from the
original drawings. The existing grinding
machine includes both metric and imperial
Corus Northern Engineering Services
(CNES) has built and installed a large
grinding machine for Wyman-Gordon Ltd,
a manufacturer of seamless pipes for the
offshore oil, gas and power generation
industry, based in Livingston, Scotland.
The new grinding machine, which measures
19m in length by 2.5m wide and 4.5m high,
weighs approximately 70 tonnes and has
a 16m travel for the grinding heads. The
machine will supplement the company’s
original grinding machine, which is more
than 40 years old and will help to reduce
lead times for process pipe.
The new grinding machine will be used to
grind the outside diameter of seamless
pipes, which vary in length from 5m up
to 12m, with diameters from 200m up to
1,200m (as long as the weight does not
exceed 15 tonnes). The grinding machine
grinds the outside casing to give a smooth,
flat finish to the pipe.
Wyman-Gordon manufactures a range
of class 1 rotating parts for military, civil
and industrial gas turbine applications.
Tungsten carbide
insert for outside
tube scarfing
HSS-DMo5 saw blades
& friction circular
saw blades
CON.T.R.A.S.T.
Impeder core for
high frequency
welding of tubes
Fiberglass pipes
for impeder
core
www.contrastsale.com info@contrastsale.comCON.T.R.A.S.T.
30026 PORTOGRUARO - Italy - Via Umbria, 15
Tel. ++39.0421.271699 Fax ++39.0421.770571
New grinding machine for seamless pipe manufacturer
CNES has installed a new grinding machine for
Wyman-Gordon