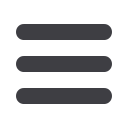

N
ovember
2008
www.read-tpt.com38
T
echnology
U
pdate
›
Khartsyzsk Tube Works has recently undertaken a
major reconstruction project
Completion of technical reconstruction at
Ukrainian tube works
The tube works includes two new mills for
welding inner weld seams on large diameter
pipes. The supplier of this equipment was
Uhrhan & Schwill, Germany, an expert in
electroarc automatic welding.
The new mills provide welding of the inner
seam by three arches on pipes of Ø406-
508mm and by four arches on pipes of
Ø508-1,422mm, with wall thickness from
6mm to 40mm.
A new non-destructive ultrasonic control
unit (SNUL-Echograph 1155-3L-1Lm-1T)
from Karl Deutsch, Germany, has also been
put into operation. The system allows the
achievemement of welded seams on pipes
406mm to 1,422mm in diameter, with wall
thickness from 6.3-40.7mm.
Khartsyzsk Tube Works
– Ukraine
Fax
: +380 6257 45695
:
marketing@ukrpipe.com.uaWebsite
:
www.ukrpipe.com.uaKhartsyzsk Tube Works (KhTW), Ukraine, is
carrying out a major technical reconstruction
of its manufacturing facilities, with the
building of a new line in its no 2 welding
workshop.
Preparatory construction work began in
March/April 2006, and all equipment has
now been installed in the welding workshop.
The new line contains a milling machine for
plate edge trimming from Linsinger, Austria,
and a three-roller mill, post-forming machine
and tack-welding machine from Haeusler,
Switzerland.
Using this equipment, the company can
manufacture pipes which correspond to
all modern requirements, in particular
gas pipes of 1,220mm and 1,420mm in
diameter (48" to 56") from steel grade up to
X80 with one longitudinal seam. The total
cost of the investment project is close to
UAH 130 million.
Condat specialises in the development of
chemical products, including a wide range
of industrial lubricants. The company’s
range dedicated to tube covers the
applications of hot and cold forming for tube
and bar in rolled, drawn, formed or extruded
processes.
The extensive product range is designed
for all metals, carbon and stainless steel,
aluminium or copper as well as alloys. It
includes graphite coatings, non-reactive
pre-coatings, soap reactive coatings, dry
soap powders, soluble lubricants, neat oils,
greases and pastes, surface protection
products and degreasing products.
Condat was among the first companies to
develop a complete range of non-reactive
coatings and to offer its customers an
environmentally friendly alternative to
conversion coatings (zinc phosphate,
oxalate) for carbon and stainless steels.
For tube drawing of stainless and carbon
steel, Condat offers Supralub 35. This
coating is applied directly onto the bare
metal surface, without any previous surface
preparation such as zinc phosphate. The
eco-friendly, soap-based product does not
contain any solvents or heavy metals, and
does not produce any waste, such as zinc
phosphate sludge.
The company has also developed
a specific lubricant for carbon
welded tube. Vicafil TF 498 A
is a soluble lubricant with very
low dilution ratio, high filtering
ability and good stability. It
provides improved protection
against corrosion, reduction
of gumming deposits, clean
working environment and strong
detergent properties. Vicafil TF
498 A combines an extended ‘in
service’ life with the ability to be
used as a unique lubricant for the
whole process.
In order to replace mineral base technology
for aluminium tube drawing, Condat has
developed a fully synthetic lubricant: Vicafil
TFH 1644.
The first goal of such a product is to
enable degreasing during heat treatment,
reducing the cost of the process. Its low
viscosity avoids excessive drag out of the
lubricant, and so reduces consumption.
It also eliminates the need to use
trichloroethylene or other degreasing
chemicals, thereby completely removing
the degreasing stage, saving time and
increasing productivity.
Residual left upon the tube after heat
treatment is close to zero and no stains
remain on external or internal surfaces.
For aeronautic grades, TFH 1644 provides
temporary protection. The formulation of
the product has been engineered to be
chemically stable and user friendly, to avoid
irritation risks.
The technologies used in Condat lubricants
are also found in tube drawing and forming
processes, including specific applications
such as pilgering, or final products such as
seamless tubes.
Condat
– France
Fax
: +33 4 7807 3800
Website
:
www.condat.frA complete range of lubricants for tube applications
Lubricants from Condat