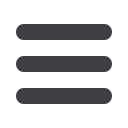

EuroWire – September 2010
68
technical article
(Restriction of Hazardous Substances)
directive, which came into force on 1
st
July
2006, bans the typical lead-tin compounds
that were formerly used. The integration
of the functional pure tin coating in the
material cycle is described in detail below.
The choice of material for connectors is
based primarily on physical criteria such
as electrical conductivity, modulus of
elasticity, thermal relaxation and pro-
cessing characteristics, ie ductility and
bendability, and welding behaviour.
Issues relating to partial or total surface
protection are of secondary importance,
as are the basic availability of the materials
and material costs.
An examination of production and
punching waste reveals that, in many
cases, it is not given the attention that,
on ecological and economic grounds,
it deserves. This is illustrated by the
following example.
During production from hot-dip tinned
CuFe2P (C19400) of large lead frames
for ABS and ESP systems about 50% to
70% scrap is produced.
None of this can be directly recycled (fed
back into the melting process). It has to go
through time-consuming smelting and be
electrochemically separated.
It is fed back into the material/production
cycles as a cathode. This procedure
is energy intensive and is, therefore,
expensive relative to direct melting.
Usually a 0.4mm thick strip is provided with
a 3μm coating of tin on both sides. When
the scrap is directly recycled, the resulting
CuFe2P alloy contains an impurity of tin at
around 1.5%.
This has a major effect on work hardening
behaviour and on the electrical conduc-
tivity of the alloy, which falls drastically
when the tin content exceeds 0.3%
(see Figure 2).
There is, therefore, a need for a new alloy
with comparable properties to CuFe2P but
which can be recycled without difficulty,
even when coated with tin. Pure copper/tin
alloys such as CuSn 0.15 have the potential
to be used as alternatives. When coated
with tin, the scrap can be fed directly into
the material cycle
(see Table 1).
Moreover, the mechanical and techno-
logical properties correspond relatively
well to those of CuFe2P.
There are, however, distinct weaknesses
in terms of softening behaviour and
relaxation resistance
(see Tables 2 and 3).
A look at the newly developed alloy BB05xi
shows a different situation. The targeted
harmonisation of the alloy elements (tin,
nickel and phosphorus) gives the material
mechanical and technological properties
comparable to CuFe2P, together with the
softening and relaxation (stress creep
of the component at high temperature)
properties profile required for further
processing
(see Figure 3)
and for the
intended application.
BB01 C14410/15
SB02 C19400
BB05xi
Copper
Balance
Balance
Balance
Tin
0.12
-
0.2 – 0.8
Zinc
<0.10
0.13
<0.05
Iron
<0.02
2.4
<0.02
Nickel
<0.02
–
0.1 – 0.6
Phosphorus
<0.015
0.03
0.008 – 0.05
BB01
SB02
BB05xi
Electric conductivity
Soft [% IACS]
>83
63
>62
Thermal conductivity
[W/mK]
360
260
250
Coefficient of thermal
expansion [Rt-100ºC]
17.7 x 10
-6
17.7 x 10
-6
17.7 x 10
-6
Elastic module
[GPa]
128
123
126
Strip thickness 0.3mm
BB01
SB02
BB05xi
Rm [MPa]
450
450
425
Rp
0.2
[MPa]
410
420
380
A50 [%]
4
9
6
HV
130
145
125
Softening temperature
[ºC (1 h)]
300
350
350
Bendability
[180º GW R/S]
1
0
0.5
Bendability
[180º BW R/S]
1
1
0.5
Tin content in %
Relative electric conductivity in %
Figure 2
▲
▲
:
Influence of the tin content on the conductivity of CuFe2P
Table 1
▲
▲
:
Comparison of the chemical composition of various bronzes
Table 2
▼
▼
:
Comparison of the technological properties of various bronzes
Table 3
▼
▼
:
Comparison of the technological properties of various bronzes