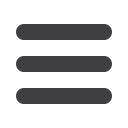
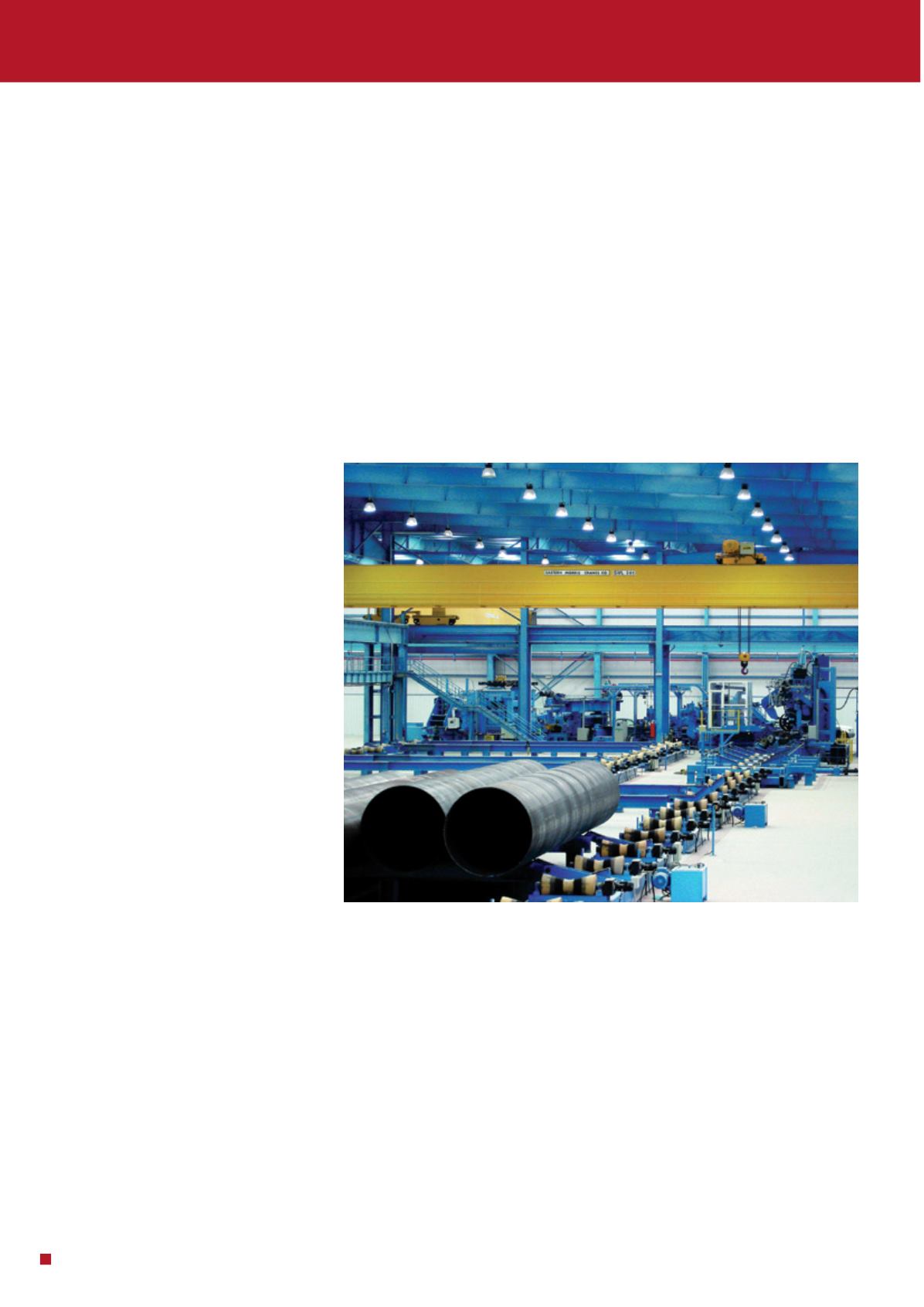
Industry News
www.read-tpt.com10
N
ovember
2012
Emulsion filtering unit sold
EUROMAQUINA
has
sold
and
successfully installed its own engineered
emulsion filtering unit FILTRA-4 at a
hydrotester in a seamless tube factory
called Tubos Reunidos in Spain. The
filtering system was developed to
have zero maintenance and very good
emulsion and process quality. It has
also been successfully installed in South
America (Brazil, Peru) and Turkey.
Other recent projects include
revamped machines sold in Germany
and France, and in emerging economies
in Africa like Egypt, Kenya and Angola.
Euromáquina recently transferred a
complete tube and pipe factory from
Turkey to Mexico, and will lead the
renewed start-up.
This kind of turn-key hand-over of
used equipment, partially including
integration with new equipment,
has so far been implemented with
annealing furnaces, slitting lines, tube
mills, finishing machines and even
galvanising plants.
Euromáquina, SA
– Spain
Fax: +34 91 658 62 08
Email:
comercial@euromaquina.comWebsite:
www.euromaquina.comLarge pipe expertise acquired
THE demand for large pipes for the
construction of pipelines is currently
growing. Schuler AG, Germany, has
reacted to this trend and expanded its
product spectrum to include turnkey
systems solutions for the economic
production of large pipes. This was
made possible by the company’s
acquisition of ATIS GmbH, an
engineering firm specialising in this
field. The respective contracts were
signed in April.
Schuler has more than 170 years of
expertise in the field of metal forming,
as well as extensive know-how in
research and development, large
equipment
manufacturing,
project
processing, and global service network.
ATIS will provide detailed knowledge
of the planning, development, delivery
and modernisation of complete pipe
equipment and systems throughout the
world. “This strong partnership offers
numerous benefits for our customers,”
said Jochen Früh, managing director of
Schuler Pressen GmbH.
Pipelines have to span huge distances
across inhospitable terrains and are
often exposed to extreme conditions.
Temperatures well below freezing and
enormous pressures, such as on the
seabed, exert huge loads on the pipes.
At the same time, the pressure inside
the pipes is being constantly raised
in order to extend the distances of the
transported materials.
“The stability and absolute quality of
the manufactured pipes is therefore all
the more important,” explained Dietmar
Rieser, managing director of ATIS.
During their manufacture, pipes are
carefully scrutinised using ultrasonic
devices, X-rays and water pressure
(with a hydrotester). There are two basic
methods for the production process itself:
“Large pipes are either welded together
as spirals from a long metal coil or
bent to an ‘O-shape’ with a longitudinal
weld,” explained Manfred Wischnewski,
managing director of Schuler SMG
GmbH & Co KG.
Spiral-shaped
pipes
can
be
manufactured in lengths of up to 24m,
with diameters of 450 to 3,500mm and
wall thicknesses of 6 to 25mm. The
forming and welding stages can directly
follow each other (online process).
Longitudinal weld pipes with diameters
of up to 1,625mm and wall thicknesses
of up to 65mm are produced using
either crimping presses, U-forming
and O-forming presses, or equipment
for the step forming process – such
as Schuler’s Linear Feeding J-Press
(LFJ press). Longitudinal weld pipes
are usually produced in lengths of 12
or 18m. The new LFJ press can also
produce lengths of up to 24m.
A lower-priced alternative to stainless
steel pipes, needed for the transport
of aggressive or sensitive substances,
are lined pipes – a combination of thin-
walled stainless steel and conventional
carrier pipes.
Schuler AG
– Germany
Website:
www.schulergroup.comATIS GmbH
– Germany
Email:
info@atis-germany.deWebsite:
www.atis-germany.deView of a spiral pipe plant