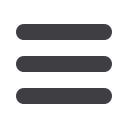

50
Wire & Cable ASIA – January/February 2017
www.read-wca.comFrom the Americas
expects demand in China to have fallen only one per cent
to 665.6mmt for the year. It sees Chinese demand falling
two per cent to 652.3mmt in 2017. Worldsteel, formerly the
International Iron & Steel Institute (IISI), said the $900 billion
global steel industry remains vulnerable to geopolitical
and economic uncertainties. In particular, T V Narendran,
chairman of the Worldsteel economics committee, told
Reuters
in Dubai (11
th
October), “Downside risks come from
the high corporate debt and real estate market situation in
China.”
An old but unexploited girdering system
offers new advantages for construction of
short-span steel bridges
A group of steel-bridge advocates has responded to a call
from the USA Federal Highway Administration (FHWA) for
a cost-effective accelerated bridge construction system
for steel bridges 140 feet or less in length. The Short Span
Steel Bridge Alliance (SSSBA), in conjunction with West
Virginia University (WVA) and Marshall University, a research
college, has produced a new type of tub girder that is said
to require less fabrication and installation time.
As reported by Aileen Cho of the
Engineering News-Record
(Troy, Michigan), SSSBA organised a modular steel-bridge
task group to explore possibilities, from twin-tub girders
to orthotropic decks. The group, made up of more than 30
partners from the steel industry, academia, government
organisations and bridge owners, developed the
pressed-brake tub-girder (PBTG) system in three years.
The system is described as consisting of shallow, modular,
galvanised trapezoidal boxes fabricated from cold-bent
structural steel plates. The concrete deck is precast on
the girder and the modular unit shipped by truck to the
bridge site. (“Industry Group Introduces a Pressed-Brake
Short-Span Steel-Girder System,” 12
th
October)
SSSBA fabricates its girders from standard steel plates,
typically 72
"
or 96
"
wide, supplied by a mill. Greg
Michaelson, an assistant professor at Marshall University
(Huntington, West Virginia), said a plate is hit with a press
brake four times – twice on the ends and twice in the centre
– to achieve the U-shaped tub. With shear studs on the top
flange and diaphragms, the concrete deck completes the
composite unit.
The concept of a pressed-brake tub-girder system was not
new but had not been fully developed, said Karl Barth, an
engineering professor at WVU. “What we’re doing is taking
all the advantages of a large, deep, welded tub girder and
scaling [it] down to a short-span bridge system,” he told
Ms Cho. “All the bracing, welding, and other details that
go into a large tub girder simply couldn’t be economically
deployed in short spans.”
According to the SSSBA, cold-bending of the section –
instead of cutting and welding – delivers as much as a
50 per cent reduction in fabrication costs, compared to
proprietary cold-formed box-girder systems. There are
economies, as well, in fewer stiffeners and cross frames,
the group said. And the girders can be used for both
tangent and skewed configurations.
Dr Barth noted that, while cold-bending steel fabricators
often make crane booms and utility poles, they are not
necessarily traditional bridge fabricators. Thus, he said,
the PBTG system could create a new business line for
operators of large press brakes.
Elsewhere in steel . . .
Steelmaking is returning to the southeast of England:
specifically to the Sheerness plant in Kent which was
closed down in 2012 but is to be restarted by the
industrial group Liberty House. Having signed a long
lease with Peel Ports, owner of the site, Liberty intends
to have the rolling mills at Sheerness – with capacity of
750,000 metric tons a year – back in production by the
summer.
As reported by Alan Tovey of the
Telegraph
(14
th
October), the Sheerness news came almost exactly a
year after the company reopened a steel mill in Newport,
South Wales; and two weeks after it restarted the Dalzell
works – Britain’s largest steel plate mill – near Glasgow,
acquired from Tata which had intended to phase out
production there.
Liberty was understood to be planning to relocate the
electric arc furnace from Sheerness to the Newport
plant. V B Garg, CEO of Liberty Steel Newport, told
the
Telegraph
that the decision to keep the rolling mills
at Sheerness, rather than moving them elsewhere, was
dictated by considerations of cost and the prospect
of “[allowing] us to take advantage of emerging
opportunities in the market.”
Telecom
New Los Angeles-to-Hong Kong subsea
cable will allow users to choose from
a variety of interoperable network
equipment
Chris Preimesberger reported on
eweek.com(12
th
October)
that the “head-butting” USA online advertising rivals Google
and Facebook, whose campuses are located only a few
miles from each other on San Francisco Bay, are going
into the fibre optic cable business together. The two web
services giants are working together to lay a cable between
Los Angeles and Hong Kong that will serve their users on
both sides of the Pacific; and, eventually, perhaps transport
data from public and/or private data networks.
According to Brian Quigley, Google’s director of networking
infrastructure, the new Pacific Light Cable Network (PLCN)
will have 7,954 miles of fibre and an estimated cable
bandwidth of 120 terabits per second (Tbps). This speed
is double that of the current highest-capacity trans-Pacific
route FASTER – a Google-backed cable system which
connects hubs on the USA West Coast with Japan and
elsewhere in Asia. The other members of the FASTER
consortium are China Mobile International and China
Telecom Global (both Hong Kong-based), Global Transit
(Malaysian), KDDI (Japanese), and SingTel, of Singapore.