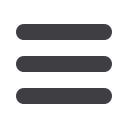

55
www.read-wca.comWire & Cable ASIA – January/February 2017
Introduction
Ultimately, every cable manufacturer aims to make a
quality product using the least amount of resources in the
fastest time. To do this, they must understand the critical
parameters that affect the strand they wish to make.
Once this is accomplished, finding the hardware to provide
them with the most flexible and effective process is
relatively easy.
The aim of this paper is to present a technological solution
in the process of the manufacture of compact conductors,
which brings cost savings from the wire drawing process
through the cabling and into the extrusion process.
This is the use of the roll form technology, which allows
the use of a single input diameter wire to be utilised
throughout the stranding process, giving significant
process savings and advantages.
Traditionally, a finished stranded conductor requires its
own drawn wire diameter. Each wire diameter typically
requires a new string up in the wire drawing machine.
Some conductor designs require more than one drawn
wire size.
Similarly, multiple set-ups in the stranding process are
necessary for each size of conductor. The set-up time
taken on both the drawing and stranding machines,
combined with inventory levels that are necessary
to manage the number of wire diameters, represent
unnecessary activities that add to the conversion cost
from rod to strand.
The SIW mentality effectively eliminates much of this
unnecessary activity associated with the traditional set-up
by using the same drawn wire diameter to finish a range of
stranded conductors.
The result is:
• Increased wire drawing output
• Reduced wire drawing die inventory
• Reduced scrap
• Significantly lower work in process
• Minimum strander payoff changes
• Increased strander output
• Shorter lead times
• Enhanced JIT manufacturing mentality
• Streamlined overall stranding process
Probably more to the point is a significant reduction in the
variables that the manufacturer needs to manipulate in the
manufacture of any strand programme.
The change in philosophy that is required to effectively use
single drawn wire diameter to produce the required range
of finished strand conductors is to replace the flexibility
of stranding the same number of wires using different
diameters with stranding different numbers of wires using
the same wire diameter.
In general, the benefits of the SIW mentality are
independent of the strand manufacturing process used.
It is only when the specific strand designs have been
defined and the production requirements of those
designs are determined that the choice of the optimum
manufacturing cell can be considered.
Manufacturing of
compact conductors,
highlighting the benefits
and potential cost
reductions in the whole
stranding process
By Sean Harrington, Ceeco Bartell Machine Systems LLC