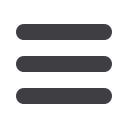

57
www.read-wca.comWire & Cable ASIA – January/February 2017
Due to the wide variety of strand that is used in the
industry, Ceeco Bartell has developed a mathematical
model to assist with the strand design.
This model uses theoretical and quantitative data that
allows prediction of the resistance of the strand. This
program further analyses the geometry of the strand to
optimise the performance of the machine. The result is an
accurate prediction of the finished strand resistance.
Figure 2
shows a cross section of a 150mm
2
strand,
showing how this program assists in the development of
the optimum strand design.
This roll form programme provides the greatest potential
as it has the smallest strand diameter schedule for a
specific stand size. Consequently this also represents
the greatest potential for insulation savings for a given
insulation thickness.
This can be clearly seen in
Figure 3,
which shows savings
in insulation while producing 95mm
2
XLPE product with
fill factors ranging from 86 per cent to 96 per cent. As the
conductor becomes smaller and the interstices disappear,
the amount of insulation used will be reduced. 92 per cent
fill factor is the best compaction that can be achieved
using conventional methods. However, with the roll forming
process 96 per cent fill factor can be achieved. This
creates a potential saving of material of around two per
cent.
The productivity of the extruder relies in part on the
integrity of the strand construction. This applies equally to
low, medium and high voltage extrusions.
Unstable strand construction not only compromises the
speed of the stranding and extrusion processes, but can
lead to considerable losses due to scrap and down times
for both lines.
Birdcaging is often the result of unstable strand design.
A tightly wound conductor is less likely to end up
birdcaging. The tightness of the strand is greatly
dependent on the geometry of the elements.
For this reason, the lay of the conductor is important. The
elements of unilay/unidirectional lay conductors are nested
and, therefore, inherently have a smaller outer diameter
than reverse concentric lay and SZ conductors.
In addition, unilay/unidirectional lay conductors self-tighten
under tension. As a consequence of this self-tightening
feature, the extrusion of unilay/unidirectional lay conductors
is statistically less prone to birdcaging.
The surface of the strand is also critical. A smooth outer
layer such as one found with a roll formed layer presents a
clean round profile to the extrusion process and, therefore,
minimises the accumulation of conductor dust during the
extrusion process.
The process is shown in
Figure 4
. Round wire is taken from
large coil packs and passes through the roll form section
where its shape is changed into various roll form profiles
that are then assembled at high speeds by either a double
twist machine or a single twist machine, depending on
product size.
This high-speed continuous process allows for linear
speeds of 200m/min to be achieved while producing highly
compact conductors. The roll form strander is capable
of producing 40 tons of 150mm
2
compact aluminium
conductor in a 24-hour cycle.
Conclusion
Savings in production costs depend on many factors
such as existing manufacturing facilities; whether the
strand is currently manufactured in-house or purchased;
the care and control exercised over input copper and
aluminium wire; general house-keeping; and the control
of high-speed double twist stranding machines. Under the
most advantageous conditions savings can provide quite
astonishingly short pay-back periods, but should of course
be calculated for each individual application.
The high performance of a roll form strander coupled with
the Ceeco Bartell roll forming process will allow the cable
manufacturer to reduce costs without compromising the
finished conductor performance. An awareness of this
and other new technologies, combined with enlightened
specifications, will further enhance the development of
strand design and the potential to optimise further the
manufacture of stranded conductors.
Ceeco Bartell Machinery Systems LLC
Ceeco Bartell Products
400 Applewood Crescent,
Suite 100, Vaughan,
Ontario, Canada
Tel
: +1 905 761 3000
:
sales@bartellmachinery.comWebsite
:
www.bartellmachinery.com❍
❍
Figure 4
Double
Twist
Roll
Forming
Coil Pay
off
Assembly into
Compact
Conductor
Roll Formed
Profiles
Round
Wire