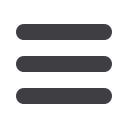

56
Wire & Cable ASIA – January/February 2017
www.read-wca.comIt should be noted that the concept of using a single
input wire to manufacture a range of finished conductor
sizes is not new; it is used within the confines of most
manufacturing plants within the allowances of the current
specifications.
It has been used extensively in Europe where strand
programmes using the single input wire diameter to cover
a range of finished conductor sizes has been in existence
for decades.
The potential cost reductions using this process can be
split into the following areas:
• Process savings
• Material savings
Process Savings
The obvious impact of the incorporation of roll forming into
the stranding process is shown in
Figure 1
.
While still working within the constraints of the IEC
and ASTM standards, the roll forming process allows
the number of wires required to produce a range of
conductors to be reduced dramatically.
In this case, to cover 35mm
2
to 240mm
2
the number of
wires has been reduced from eight to two.
In a similar way, 35mm
2
to 500mm
2
the number of wires
can be reduced from 12 to three. This reduction in the
required number of wire sizes brings about major cost
savings in the wire drawing area:
• Creates a higher productivity in the wire drawing
machine due to the elimination of multiple set-ups for
the different wire diameters required for the traditional
strand designs
• Reduces the amount drawn wire scrap through wire
size changeover
• Creates a reduction in the wire drawing die inventory
Similarly the roll forming process has a cost saving impact
in the stranding process:
• Lower volume of different wire sizes being produced to
await the stranding process
• Ability to use larger package sizes and switch from a
bobbin system to a stem pack system
• A reduction in down time due to loading, with the ability
of automatic pay-off changeover while the machine is
running
• Quicker set-ups for different strand sizes due to the
elimination of the movement of different pay-off sizes
• Higher linear production speeds, when compared to
conventional stranding methods
• Reduction in manning levels in the stranding process
Material Savings
The challenge for today
’
s manu-
facturers is to determine what target
is to be chosen within the scope of
the specifications. If the criteria for
determining the construction were
based solely on the economics,
the industry would gravitate to the
unilay conductor schedule, and the
smallest diameter that is allowed
within that schedule.
The roll form process allows unilay products produced up
to 500mm
2
. Statistical analysis of strands compacted with
methods (die or rollers) other than the roll form system has
shown that a typical material variance of ±1% to ±1.5%
must be expected.
These results, therefore, lead to the need to oversize the
conductors by at least three per cent in order to ensure
that product does not fall below specification. This excess
material is, effectively, given to customers free of charge.
When utilising the Ceeco Bartell roll form system with its
strand design software, the material variance is reduced
dramatically.
Giving a real and very tangible material saving over
conventional compacting methods, this is particularly
important with the current cost of aluminium and copper.
This means that the minimum diameters specified in the
IEC and ASTM standards can be achieved, while at the
same time approaching but not exceeding the maximum
resistance.
❍
❍
Figure 1
8 wire sizes required using conventional system
2 wire sizes required using SIW system
❍
❍
Figure 2
:
Strand simulator output 150mm
2
compact strand
Economic analysis of 95mm
2
XLPE product
Fill factor
86% 92% 96%
Configuration
1=6=13 1=6=11 2=6=9
Outer diameter
(mm)
11.7
11.39 11.07
Outer gap area
(mm
2
)
15.88 0.710 0.663
Insulation cos
t
(US$/km)
131.35 109.55 106.83
❍
❍
Figure 3