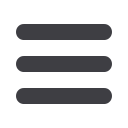

End Users/Operators
By the period 2005 – 2012 most major end user operators in oil and gas at least, had set up global
safety groups to investigate, act and improve on internal standards, guidelines and procedures. No
small task and their role often misunderstood by the sites, who often kicked back with the ‘not
invented here’ or ‘this is the way we’ve always done it’ mentality.
In an internal enquiry to a release at a UK refinery where the HSE had visited the site and asked for
their Functional Safety Management Plan, the site personnel had no answer. In fact, not only had they
never heard of such a document or the philosophy underpinning any such plan but were still
convinced that their MOC procedures were good enough and their own tried and trusted processes
could only be compromised by this FSM plan!
But that was somewhere in the 2005 – 2012 period. Where are we today? Are we any nearer an
accurate ‘big dial’ safety reading on a day by day basis? Do we have to be? In order to answer this
question let us look at what has been a successful and growing practice, asset assurance or asset
integrity management with what we see today as functional safety management.
If we compare 1. Asset integrity vs 2. Safety assurance:
1.
We plan, we inspect, we maintain, we test, we report, we analyse, we improve. The result
being less failures, less outages, optimised plant, better returns on investment.
2.
The right people, in the correct roles with maintained competency, plan, verify, inspect,
maintain, test, report, analyse, improve and are assessed and audited and the risks are re-
assessed on a 5 year basis. The result being less failures, less outages, optimised plant, better
returns on investment, no environmental damage, no plant loss, no injuries, no deaths, no
damage to reputation.
Sadly the budget holders in many organisations see no difference between 1 and 2, leaving an often
overworked operations and maintenance team to figure out how to do two jobs at the same time. The
business of asset management has evolved over time, processes and procedures, data handling and
reporting have grown with the company’s process automation and business systems. Asset assurance
or integrity management, is a clear winner, with readily available cost/performance/ROI matrices.
It is of course, a much easier argument for an executive committee to grasp; no gas turbine, no
compressor = no plant production = no ROI = no bonus.
The cost of third party service and maintenance of major assets such as turbines and compressors is
astronomical but also justifiable when placed alongside total plant shutdown costs. So the investment
is there every year without question.
What of safety management? It’s made to fit to the current systems and mindsets. The technical
challenges, the expertise and experience, maintenance, modifications, proof testing, the analysis and
assessments and audits, training and competency, all now stored in numerous silos of data such as
Management of change;
alarm management;
historians;
maintenance or business software;
schedules;
action tracking, etc.