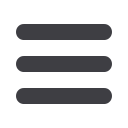

The list above and many more islands of data collection all evolved over years but for something that
isn’t quite safety related but will just have to do. With such disparate repositories for data and the
extra time and cost, safety related tasks may remain open, reports unfinished or worse unread and
therefore how can analysis and improvements be achieved? How can we really understand our
vulnerability to major accidents?
If safety related activities are slipping because of time i.e. engineers being too heavily laden with
tasks across the plant, then what is the cost and how does that apply to any ROI if we employed more
technicians or better still, empowered them with a software based safety lifecycle management tool?
Improved production and bottom line are easier to track and traceable back to enhanced maintenance
and operation. It is much harder to prove success against major accidents that haven’t happened and
may never happen. Even spurious trips and unplanned outages due to safety related systems and
operations have a cost impact are all too often, once fixed and blame applied, soon forgotten and no
investment forthcoming.
‘Where’s the bang for my buck’, your spendthrift executive may well ask? Well with no buck, trust
me, the bang may well be on its way!
Investment in safety is pretty low on the list compared with asset integrity and yet it is exactly the
same investment but with better results (or much worse consequences). If we look at the report below
we can ask the question ‘have attitudes improved any in the last eleven years’?
From the COMAH Buncefield report:
Buncefield; Why did it happen?
Hon Mr Justice Calvert-Smith, commented that cost cutting per se was not put forward as a major
feature of the prosecution case, but the failings had more to do with slackness, inefficiency and a
more-or-less complacent approach to matters of safety.
From the Executive summary:
This report does not identify any new learning about major accident prevention. Rather it serves to
reinforce some important process safety management principles that have been known for some time:
There should be a clear understanding of major accident risks and the safety critical equipment
and systems designed to control them.
This understanding should exist within organisations from the
senior management down to the shop floor, and it needs to exist between all organisations involved in
supplying, installing, maintaining and operating these controls.
There should be systems and a culture in place to detect signals of failure in safety critical
equipment and to respond to them quickly and effectively.
In this case, there were clear signs that
the equipment was not fit for purpose but no one questioned why, or what should be done about it
other than ensure a series of temporary fixes.
Time and resources for process safety should be made available.
The pressures on staff and
managers should be understood and managed so that they have the capacity to apply procedures and
systems essential for safe operation.
Once all the above are in place:
There should be effective auditing systems in place which test the
quality of management systems and ensure that these systems are actually being used on the
ground and are effective.
At the core of managing a major hazard business should be clear and positive process safety
leadership with board-level involvement and competence to ensure that major hazard risks are
being properly managed