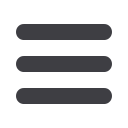

These findings from an incident in 2005 still reflect on the challenges safety related personnel face
today. So how can we create an environment and plan maintenance, inspection and testing activities
that will realise good data that once analysed will verify that the target risk reduction (whether it be a
SIL or a combination of other measures/metrics) is achieved and continues to be achievable?
As argued earlier in this section, attempts to execute, collate and store some of the above items may
well be partially achievable within existing company processes and procedures and possibly part of a
DCS or SAP driven maintenance management system. But what happens when a new project is
undertaken and the numbers from the risk assessment report and the requirements of the SRS are
received? Which in themselves are often the results of a series of meetings that:
did not include operations personnel;
where specifications were created by software tools by others
o
in a format not in line with the sites other data
o
delivered in PDF format
o
that have no use during later phases;
that did not include real consideration for
o
operating conditions
o
maintenance overrides
o
modes of operation
o
proof test intervals
which are not easily transferrable to existing system;
and may require manual input (so never gets done or increases errors)
If we remember the HSE book ‘Out of Control’ there is room enough above for a whole host of
systematic errors to be introduced before we add a large slice of the 44% of errors introduced during
the specification phase for functional logic not covered by the SRS.
Add to this the description of functional safety from IEC61511-1 2004
3.2.25 functional safety; part of the overall safety relating to the process and the BPCS which
depends on the correct functioning of the SIS and other protection layers
Therefore, to manage
functional safety
we must manage and maintain all aspects of people, procedure,
plant and planning to achieve the
correct functioning of the SIS
at all times. This is becoming a hard
task for today’s professionals when we consider all the disconnects and disparate systems and silos of
information described previously. Remember also the correct functioning of other protection layers as
the SIF only needs to provide a certain risk reduction if the other measures “pull their weight” i.e.
perform as predicted – this is the intimacy of process and functional safety.
If we again turn to LinkedIn and search through end users companies in hazardous industries for
personnel with process or functional safety titles. Such a search through COMAH registered
companies in the main unearths quite a few individuals, which is good. The fact that most have held
such a position for only a year or two is understandable.
However, questions have to be asked; are systems in place that assist functional safety? Have roles
been identified, personnel assigned, gap analysis undertaken, safety activities defined and assigned? Is
there a functional safety management plan document? Are activities tracked, reports approved,
assessments undertaken, non-conformances resolved? Have procedures been modified? Is
maintenance during operations risk assessed? Is information reporting and data shared and analysed
efficiently?
Unfortunately, if ‘rabbits’ and ‘head lights’ comes to mind. Unfortunate in that in order to have a
working, tried and tested system with a good team working in unison as part of a company wide effort
possibly another 5 years have gone by or even longer.