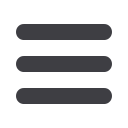

EuroWire – September 2009
52
Steel wire, cable & rod
MELC straightening method and machinery
Eurobend SA first developed the hyperbolic roller rotor during the ‘80s in order to replace the conventional die rotor. The method
is based on the rotor straightening system but, instead of dies, places hyperbolically profiled cylinders (rollers) made from coated
steel. The cylinders execute the two fundamental operations of straightening and feeding the rod simultaneously. Eurobend has
straightening and cutting machines capable of handling up to 28mm diameter products.
The advantages of the method, other than straightening quality and consistency, are said to include:
Minimised machine downtime, since continuous adjustment of the straightening mechanism is not needed. If a rotor operates
•
with the same wire diameter the average life of the rollers is believed between three and five years, depending on wire or re-bar
quality and properties
Straightening of high tensile steel (up to 1,800 N/mm
•
2
UTS) is possible, and at a lower cost
Cutting of the required length is achieved with flying shear cutter, while the wire is moving, without having to start and stop, or to
•
slow down the speed of the wire in order to cut
The simplicity of the design allows for the
construction of multi-head machines, ie up to
six rotors (straightening and cutting lines) can
be fitted on a single machine body, depending
on the productivity requirements and the
diameter ranges of each customer. Each line
works independently from the others or in any
combination or all together. Each has a dedicated
collector bin and can cut the same or different
lengths. Applications for the system include
machines processing wire, PC wire, all rebar
grades, stainless steel rebar and copper coated
high tensile wire for lightening rods.
Eurobend SA – Greece
Fax
: +30 210 620 6567
:
eurobend@otenet.grWebsite
:
www.eurobend.comMELC six line straightening and cutting machine from Eurobend
▲
▲