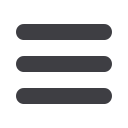

EuroWire – July 2008
40
english technology news
This year marks the 30
th
year of trading
in the UK for Lee Spring Ltd and sees the
introduction of two new spring products:
constant force springs and REDUX™ wave
springs. Both spring types are offered
from stock and can be custom designed
to suit particular applications.
These products increase Lee Spring’s
portfolio to over 15,500 different types of
stock spring.
Manufactured from high yield 301
stainless steel strip the constant force
springs exert a near constant restraining
force to resist uncoiling. This natural
inbuilt stress resists load at an even
rate and makes them suitable for use in
retractor mechanisms.
Common
applications
include
counterbalance springs, car seat belt and
cable retractors.
Constant force springs are usually tightly
coiled on a drum and either the free end
or the drum can be attached to the load.
Four life cycle ranges are offered: 2500,
4000, 13000 and 25000 covering loads
from 1.02 to 73.42N (0.23 to 16.50lb).
Lengths vary from 356 to 1524mm
(14" to 60"; thicknesses from 0.10 to
0.51mm (0.004 to 0.020") and widths
span the range 6.35 to 31.75mm (0.250 to
1.250").
Wave springs perform a similar function
to compression springs but use less
height space due to a sine wave design.
Produced in stainless steel type 17-7
PH Lee Spring’s REDUX™ wave springs
can be used in static or slightly dynamic
applications where space or radial and
axial tolerances are tight.
They also offer greater control of axial
movement and consistent load transfer.
Stock sizes range from rod sizes of 6.35
to 25.40mm (0.250 to 1.0") to suit hole
diameters from 9.53 to 31.75mm (0.375
to 1.250") and in spring rates from 1.58 to
52.21N/mm (9.00 to 298lb/in).
Lee Spring Ltd – UK
Fax
: +44 118 977 4832
:
info@leespring.co.ukWebsite
:
www.leespring.com30 years of spring
Roland
Electronic
GmbH has introduced
the newly designed
digital UFD40 system
as a successor to its
proven analogue UFD
detector.
The system has been
designed to detect
faults in butt welds
and mechanical con-
nections
in
wires,
cables and small tubing
made
of
metallic
materials such as steel,
stainless steel, copper,
brass and aluminium.
UFD40 is based on the eddy current
measurement principle; the material to
be monitored passes through the orifice
of an encircling coil sensor.
Roland Electronic offers sensors suited
for materials ranging in diameter from
1mm to 90mm. The UFD40 has features
typically available in classic eddy current
fault detection systems designed for
automated
production
processes,
including
adjustable
frequencies,
high and low pass filters as well as
y-component and vector analysis.
This makes the system suitable to
monitor many different discontinuities
with one type of hardware.
UFD40 is of a modular design and offers
several operating modes. The complete
electronic circuitry for two independent
measuring
channels
is housed in one IP65
module
enclosure.
Each channel auto-
matically
executes
the
measurement
functions. The RS232
interface provides the
connection to the host
PC, which serves as
the operating interface
for the system and
provides visualisation
of all measurement
values.
Both measuring chan-
nels function autonomously, allowing
the disconnection of the host PC.
A parallel interface and fieldbus inter-
face are available for communication
with the production equipment PLC.
Roland Electronic GmbH
– Germany
Fax
: +49 7236 9392 33
:
info@roland-electronic.comWebsite
:
www.roland-electronic.comAnalogue steps aside for new UFD40
Among the products displayed on
the Wieland-Werke AG stand at wire
2008 was its range of electronic wires,
manufactured from high-performance
copper alloys to combine the
counteracting properties of high
conductivity and high strength.
Special heat treatments and the
addition of special alloying elements
enable copper to resist alternating
load, to transfer high currents and to
withstand long-term high temperature
operation without being subjected to
high stress relaxation.
The materials K55, K65, K80 and K88
are used in connector pins, canted coil
spring connectors, fatigue-resistant
strands and high tension magnet wire.
Another new product on the stand was
rectangular (flat) wire, tin coated by
hot-dip tinning. This tinning method
improves
resistance
to
whisker
formation in electrical contacts.
Wieland-Werke AG – Germany
Website
:
www.wieland.comWieland at wire
Roland's digital UFD40 system succeeds the analogue UFDr
▲
▲