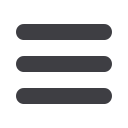

EuroWire – July 2008
37
english technology news
Shot peening for valve and
small pressure springs
Harmonious future
for OTA technology
OTA technology from Ernst Koch GmbH &
Co KG is said to guarantee a particularly
high quality product, and is especially
suited for the production of spring steel
and music wires.
Twenty-five of the machines have been
supplied in the two years since the
introduction of this new speed control
technology. The OTA lines work without
tuner and dancer rolls and thus ensure a
linear wire passing from the first drawing
block up to the spooler.
“We've noticed a continuously growing
demand for the OTA machines since the
introduction of the OTA technology,“
commented managing directors, Jochen
Koch and Thomas Voss. “With the OTA
speed control technology we've improved
the productivity of our drawing machines
by means of higher drawing speeds and
longer operation times of the drawing
dies on the one hand and achieving
better quality results on the other hand.”
The OTA lines are available in different
sizes and models, and are suited for the
processing of low and high carbon steel
wires as well as of stainless materials.
Ernst Koch GmbH & Co KG – Germany
Fax
: +49 2372 985 167
:
sales@koch-ihmert.deWebsite
:
www.koch-ihmert.deAt 600 metres long and a voltage
of 138 kV, Nexans has claimed two
world records for a superconductor
cable incorporated in a power grid.
The
world’s
longest
and
highest-voltage
superconductor
power transmission cable has been
successfully energised in a test
installation for the Long Island Power
Authority (LIPA), one of the largest
municipal electric utilities in the US.
The 600-metre, 138 kV, 574 MVA
power link, comprising three high
temperature superconductor (HTS)
cable phases running in parallel,
is the world’s first superconductor
cable system installed in a live grid
operating at transmission voltage.
Nexans – France
Fax
: +33 15669 8484
:
nexans.web@nexans.comWebsite
:
www.nexans.comWorld’s first...
Proton has launched three models of
non-contact laser doppler wire and cable
speed/length measuring sensors. These
sensors are a direct replacement for all
cumbersome mechanical wheel or belt type
cable length counters, and are wear-free.
In addition the sensors deliver a host of
interfaces including incremental Pulse O/P’s,
profiBUS, RS232, CanBUS, Ethernet IP and
deviceNET.
In any cable factory there are material losses incurred of 1-2%, the result of shortages
and over-lengths between intermediate processes, and the ‘giveaway over-length’ at
final shipping. By offering three different sensors, Proton aims to supply a solution for
“everything that moves in wire and cable,” including applications that are difficult or
impossible to measure using mechanical length counters.
By supplying every unit with a European wide recognised UKAS Certificate of
Calibration, the Proton InteliSENS offers not only a system that is calibration-free but
also has European Wide Traceability of Calibration.
Proton Products Europe NV – Belgium
Fax
: +32 52466 313
:
d.buelens@protonproducts.comWebsite
:
www.protonproducts.comProton’s InteliSENS for cable measurement!
▲
▲
Non-contact measurement
using Proton's InteliSENS
Using the RDS shot peening system,
shot peening of coil springs can be
integrated into continuous production
lines.
In RDS-Mini shot peening systems,
single
work
pieces
travel
on
horizontal rolls through the machine
at a throughput rate of over 5,000
springs an hour. Springs are fed to the
machine individually on a straight-line
conveyor, or other loading system, and
then moved through the blasting zone
on continuously rotating horizontal
rolls.
Cams attached to chains effect the
necessary axial movements.
Inside the blasting zone, the springs
are guided by adjustable baffle plates,
which also serve to focus the shot
stream on the work pieces for optimal
exposure within the ‘hot spot’ of the
blast pattern.
The parameters of the shot peening
process, including shot quality, blast
wheel speed/throwing velocity, the
speed at which the work pieces rotate
and dwell time, can be regulated to
suit the specific type of work piece, and
it is this definition of all parameters
that ensures process-safety.
Process parameters can be recorded in
the control system and retrieved when
necessary.
DISA Industrie AG – Switzerland
:
hansjoerg.stoll@disagroup.comWebsite
:
www.disagroup.comRDS-Mini shot peening system
▲
▲