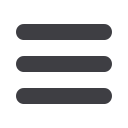

EuroWire – July 2008
42
english technology news
Current issues at Cables 2008
Pressure Welding Machines (PWM),
manufacturers of high-performance cold
welding equipment and dies, launched a
new version of its best-selling HP100 air/
hydraulic cold welder at wire 2008.
The new HP100 auto model can be used
in either normal or automatic mode. In
normal mode, the operator loads the
material and then presses the foot pedal
four to six times to activate the multiple
upset process and complete the weld.
In automatic mode, the operator simply
loads the material, presses a button and
the machine does the rest.
In either mode, the HP100 auto
guarantees consistent high quality welds
on non-ferrous materials within a range
of 1.00mm to 5.00mm (0.039" to 0.197").
The powerful solid steel welding head is
mounted on an ergonomically designed
trolley with a sloping platform that gives
the operator a clear view of the weld
area. Power consumption is minimal, and
in operation the HP100 auto requires
only a supply of compressed air and an
electric power source.
Steve Mepsted, managing director of
PWM, said: “The HP100 has been one
of our best-selling models for the last
five years. It's economical and can be
wheeled to the weld area.
“In automatic mode, the machine
provides wire and cable manufacturers
with an effortless way of welding copper
and aluminium wire and strip.
“Ideal for high cycle welding, the HP100
auto can be used to recycle short
lengths of wire that might otherwise
be discarded because they are too
time consuming to weld, so helping
manufacturers to reduce wastage and
material costs.”
PressureWelding Machines – UK
Fax
: +44 1233 820847
:
pwm@btinternet.comWebsite
:
www.pwmltd.co.ukCold welding went automatic at Düsseldorf
The 8
th
AMI international conference,
Cables, held from 15
th
to 17
th
April at
the Maritim Hotel in Cologne, was
applauded as “the most successful ever.”
AMI Consulting‘s Kerry Satterthwaite
presented an overview of the European
cable
industry,
concluding
that
restructuring in the European cables
extrusion industry has paid off with a
dramatic improvement in profits for 2007.
Primary focus of the conference was
flame retardant performance under the
new European Construction Products
Directive (CPD). Wire and cable is now
considered a building material under new
EU legislation which classifies cables by
their fire safety performance.
Testing
protocols
are
still
being
established, explained Terry Journeaux of
Prysmian Cables & Systems. The challenge
is to develop repeatable and reproducible
standards, and he detailed the European
reaction to fire classification of cables
under the CPD in 2008.
Many kilometres of cable are used in
modern buildings and cars and, as
electrical failure can be a common cause
of ignition, cable fire performance and
flame retardancy is critical. Dr Andreas
Bacher of Wacker Chemie gave an
overview of new silicones for wire and
cable, including highlights of their
superior heat resistance.
He commented on the synergistic effect
of flame retardants, a topic also addressed
by James Innes, president of Flame
Retardants Associates of the USA.
Dr Rainer Sauerwein (Nabaltec) went
on to examine trends in new metal
hydrate flame retardants for high process
temperatures. Materials differ in different
global regions and include optimised
metal hydrate blends. His paper examined
potential future trends in flame retardants
for cable applications.
New materials for cables were introduced
at the conference including high
performance polymers for the cables
industry (Evonik Degussa), co-polyester
resins for demanding cable applications
(DSM Engineering Plastics), and recyclable
polypropylene wire for automotive
applications (Dr Lee, LS Cable Ltd of
Korea).
Dow Wire & Cable is developing new
polyolefin compounds to meet the needs
of the international cables industry.
Innovation challenges in the wire and
cable market were discussed by Robert
Tarimo, market manager from Dow
Europe in Switzerland.
Dr Susanna Lieber of the Melos/Borealis
team talked about the design of bedding
compounds, which lie between the
insulating compound and the cable
sheath. Compatibility is important and
factors that effect long-term performance,
such as plasticiser migration, have been
studied. She went on to describe how
advanced bedding compound design can
improve flame retardancy.
Dr Gunter Beyer of Kabelwerk Eupen has
been working on nanocomposite flame
retardants for the cable industry. In his
30 years of experience, layered double
hydroxides have a major synergistic effect
with halogen and non-halogen flame
retardants. They appear to act by altering
the degradation pathway and imparting
barrier properties.
Daniel Calveras of General Cable, among
the largest cable extrusion companies,
followed up by describing General Cable’s
use of nanofillers in high performance
medium voltage power cables.
Cables 2009 has been scheduled for 2
nd
to 4
th
March 2009 at the same venue.
Applied Market Information Ltd – UK
Fax
: +44 117 311 1534
:
rm@amiplastics.comWebsite
:
www.amiplastics.comThe welding head of the new HP100 auto air/
▲
▲
hydraulic cold welder