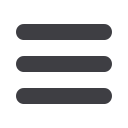

EuroWire – July 2008
33
english technology news
New Lubricant Viscosity Control (LVC)
system, used in conjunction with the
PDH ultra high-pressure lubrication
technology, can be used in the most
demanding
drawing
applications,
allowing mechanically descaled high- or
low-carbon rod to be drawn directly
at high speed, without pre-coating
chemicals.
LVC/PDH rod dry coating/lubrication
system uses three-way interaction
between the pressure, temperature
and lubricant viscosity to produce
a fusion of standard lubrication
compounds, liquefied to a viscosity
to suit the application. This eliminates
traditional pre-coating chemicals,
including phosphate and borax
pre-coating, and provides a consistent
residual coat in the first draft.
The system permits frictionless
drawing in remaining drafts with
the full lubricant film at wire-die
interface, giving physical separation
of metal-to-metal contact, in the most
demanding multi-draft applications from
rod to wire in a one-step operation.
The new rod dry coating/lubrication
system allows a wide range of residual
coats, from strongly adherent – for
high-tensile wire – to a light, water soluble
coat for plating wire.
Typical applications of the LVC/PDH dry
coating system include direct drawing
from mechanically descaled H/C rod,
without pre-coating chemicals, from
5.5mm down to 1.3mm at 18m/s, and to
3.25mm at 8.3m/s, with die life enabling
production of 200-220 tonnes/die in the
first draft.
The finishing die produces 40 to 60
tonnes of wire drawn without pre-coating
chemicals and with improved ductility,
cast and torsion.
LVC/PDH lubrication system features zero
energy consumption, self-generating
processing heat and pressure.
Decalub – France
Fax
: +33 1 60 20 20 21
:
info@decalub.comWebsite
:
www.decalub.comWire lubrication control eliminates
pre-coating chemicals
Advertorial on behalf of Decalub
Zumbach Electronics’ non-contact, on-line
measuring and control instruments.
products are used worldwide for
dimensional parameters such as diameter,
thickness,
eccentricity,
out-of-round
and for physical or electrical parameters
including expansion, capacitance and
dielectric strength.
One or more parameters on a production
line can be monitored simultaneously.
Ultrasonics
for wall thickness, with UMAC®/
•
WALLMASTER systems
up to 8 measuring points
•
up to 15,000 measurements/s
•
novel concentric transducer adjust-
•
ment allows product diameter set in
a few seconds.
Optical/Magnetic (combined)
for eccentricity/concentricity and
•
diameter, with ODEX® gauges
insensitive to wire vibration due to
•
high speed scanning
extremely compact and fully static,
•
no moving mechanisms
automatic inductor control
•
allows for installation in tight
areas
X-Ray Tomography
for wall thickness, eccen-
•
tricity, diameter/ovality with
RAYEX® Systems
high simultaneous mea-
•
suring rates, in x and y axis
unique protection system for
•
beryllium windows
customised measuring tube
•
segments
Laser
for diameter/ovality with 1, 2
•
or 3 axis ODAC® gauges
highest
accuracy,
•
repeatability up to 0.05
μm/0.0000001 in.
ultra high scan rate, up to 2,000/s
•
more than 60,000 gauges sold
•
Offering
material
savings,
process
optimisation and a fast return on
investment, Zumbach equipment ensures
the quality of wire and cable products of
any size and form, using state-of-the-art
technology throughout the range.
Zumbach Electronic AG
– Switzerland
Fax
: +41 32 356 0430
:
sales@zumbach.chWebsite
:
www.zumbach.comMultiple measuring technologies
Wire lubrication by LVC / PDH system
▲
▲
A typical gauge using each of Zumbach’s technologies
▲
▲