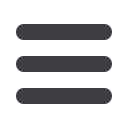

T E CHNOLOG Y
30
MARCH 2017
Welding stainless steel pipe
elbows at the push of a button
ORBITALUM Tools GmbH has further
developed its HX 16 orbital weld head
and has extended it into a series. At
the push of a button the HX 16P and
HX 22P clamp themselves on the pipe
by means of a patented pneumatic
clamping mechanism.
Through this innovation, both handling
and comfort have been improved, and
efficiency and quality of the weld result
have been increased. This makes it
possible for the HVAC industry to more
easily change over from traditional heat
exchangers made of copper to stainless
steel, which fulfils the regulations (to
F-gases directive) up to climate-friendly
refrigerants.
Stainless steel can only be joined
particularly economically, reliably and
with high quality using tungsten inert
gas (TIG) welding in conjunction with
mechanised orbital welding. Commonly
available closed orbital weld heads or
open weld tongs are not suitable, as their
construction makes placement between
the individual pipes impossible. With its
outer diameter of only 60mm, a pipe
spacing of only 30mm is sufficient for
the HX 16 for positioning and clamping
at the push of a button.
Orbitalum states that some new users
report a six-fold increase in productivity.
This makes it possible to accelerate the
procedure of aligning the weld head and
clamping the head by 10 to 15 seconds
per welding cycle; around 1.5 minutes
pass per working cycle at a pipe with
16mm outer dimension and 0.5mm wall
thickness: clamping, establishment of
the inert gas atmosphere, welding, and
cooling down in the argon atmosphere,
which prevents annealing colouring of
the weld seam.
With pneumatic clamping, the head
holds its position at the pipe elbow by
itself, rather than the operator having
to support/hold the weld head by
hand during the welding process. This
makes it possible for a less
experienced operator to
produce welds with up to
three weld heads (systems)
at the same time per cycle.
A further benefit of the
HX 16P and HX 22P orbital
weld heads is the closed
welding chamber, which
means that almost no annealing colours
can form in the heat-affected zone of the
weld seam.
All welding power sources from
Orbitalum automatically recognise
the heads and their properties, so the
operator only has to call up the specified
welding program and start the process
before beginning to weld.
The HX 16P is designed for pipe outer
diameters from 15 to 16.8mm, and the
HX 22P is for 19 to 22mm. An additional
model – HX 12P, for 9.52 to 12.7mm
diameters – will be launched later this
year.
Orbitalum Tools GmbH
– Germany
Fax: +49 7731 792 500
Email:
tools@orbitalum.comWebsite:
www.orbitalum.comA pipe spacing of 30mm is
sufficient for positioning and
clamping of the orbital weld
head at the push of a button
The HX 16P features pneumatic clamping
of the head
Photo credit: Orbitalum Tools GmbH
Photo credit: Orbitalum Tools GmbH
A new method to treat steel pipes
with respect
OBTAINING the correct mix between
experience and innovation is the
main aim of ASED, an Italian-based
brand dedicated to steel tube finishing
solutions. The company has developed
a newmethod to meet the needs of those
who want to focus on their business
without hassle and annoyances.
Maximising the efficiency of mills
means minimising waste and reducing
the total cost of ownership, but also
good organisation of working time. This
is possible in a concrete and immediate
way,
guaranteeing
customised
solutions.
Among the highlights of ASED’s range
are modularity for easy adaptability to
different kinds of production, delicacy
of movement and absence of crawling
on tubes already put into the bundle,
good functioning and maintenance
optimisation. Space saving, attention
to procedures and strong output targets
can become reality with a suitable
project plan and a wide and efficient
range of accessories to help employees.
ASED
– Italy
Email:
info@asedtubes.comWebsite:
www.asedtubes.com