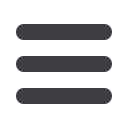

T E CHNOLOG Y
32
MARCH 2017
Straightening of zirconium
nuclear fuel clad tubing
NUCLEAR electrical power generation
reactors are powered by uranium fuel.
To separate the uranium and prevent
contamination of the reactor coolant,
the uranium fuel must be contained in
a robust environment that can withstand
the high temperatures and the intense
neutron radiation as nuclear fission
takes place.
The material used to contain
the uranium must have important
characteristics such as high thermal
conductivity, high strength, high
resistance against corrosion and high
dimensional stability. The containment
of the nuclear fuel is normally a tube
made from various zirconium alloys.
These tubes are referred to as ‘fuel clad
tubing’ or ‘fuel cladding’.
Each zirconium fuel clad tube is filled
with natural or enriched uranium pellets
and sealed. A complete nuclear fuel cell
assembly consists of a number of tubes
contained in a rigid assembly.
Extreme care has to be taken during
the manufacture of zirconium fuel clad
tubing to prevent any excessive cold
working of the tube. Cold working
causes the material to be susceptible
to hydride orientation within the high
temperature water environment in which
they operate.
During manufacture the tubes have
to be formed, finished and, at the same
time, not be subjected to excessive cold
working. The desired accuracy of tube
straightness is of particular importance
and, therefore, straightening the tube
without excessive working of the
material is challenging.
It is in this difficult nuclear arena that
Turner has succeeded in becoming a
foremost supplier of zirconium fuel clad
tube straightening machinery.
Its history in serving the nuclear tubing
industry stretches back more than four
decades, during which its understanding
of the problems and their solution have
slowly evolved.
For this challenging straightening ap-
plication the most modern ten-roll com-
puter driven machinery is now normal,
replacing older six-roll machines.
Turner has long been at the forefront
in precision straightening machine
innovation and specialised straightening
applications and has developed
important features applicable to
straightening this particular product.
These features prevent the possibility
of resulting hydride orientation in the
tube by ensuring that the amount of
pressure applied to the tube during
straightening is kept to a very low level.
Some of these features include:
special rolls which feature specific
profiled regions that reduce the amount
of friction applied to the tube as it is
straightened; load cells positioned
strategically within each roll pair, which
measure the amount of roll pressure
being applied to the tube; and
analytical software, which receives
the data from the load cells and
ensures that the amount of cold
working applied to the tube does not
exceed set points, maintaining roll
pressure at a very low, safe level.
The special roll profiles ensure
that the amount of friction generated
between the roll and the tube is kept
to the absolute minimum.
The load cells monitor the direct
pressure applied by the rolls to the tube
during straightening. Analytical software
within the computer aided setting
and management (CASAM) system
monitors the load applied by each roll
on the tube and provides control of the
machine.
The load cell signal conditioning and
amplification is carried out by highly
accurate, custom designed and built
electronic circuits.
The Turner CASAM system – now
in its third decade of operation around
the globe – has additional operational
modes and calculating algorithms
for use on this specific straightening
application.
A typical Turner ten-roll CASAM
machine for straightening zirconium
nuclear fuel clad tubing guarantees
performance on all the important
characteristics required in the final
product.
Because of the need to prevent even
the slightest marking or contamination
of the tube during straightening, the
majority of Turner machines for the
nuclear industry are supplied as
complete straightening lines including
fully integrated entry and exit tube
handling equipment.
Turner zirconium fuel clad tube
straightening machines are in use
throughout the world including China,
Korea, Sweden, Canada and the
USA.
Turner Machine Company
– USA
Website:
www.turnermachineco.comNuclear fuel clad tubing production