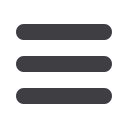

Mechanical Technology — May 2016
19
⎪
Materials handling and minerals processing
⎪
Pipe launders
make their way to chrome
M
ultotec’s pipe launders are well
known in the mineral sands and
iron-ore mining industries. The
polyvinyl chloride pipe launders have
proved their worth in these arduous ap-
plications for many years, significantly
outperforming their steel rubber-lined
counterparts. Now, chrome producers are
taking note of their benefits.
This includes Nor tham Chrome
Producers, the first chrome miner to put
Multotec’s pipe launders to the test, and
Multotec’s Graeme Smith reports that
the company will shortly be supplying an
additional 400 running metres to another
undisclosed chrome producer.
The pipe launders were supplied as
part of a spiral retrofit project at Northam
Chrome Producers’ recovery plant. A total
of 72 of Multotec’s HX5 and HX3 spirals
were designed, manufactured and installed,
boosting the plant’s recoveries by as much
as 6.0%.
The plant was using conventional steel
rubber-lined pipe launders that had been
designed for the previously installed spirals
that were also due for replacement.
Smith says that Multotec’s Technology
Division discussed the many advantages
offered by its pipe launders with the plant’s
management team. “We detailed the pro-
posed layout of the launder solutions, and
the team really liked our idea of ensuring
a more durable and tidier installation that
would also be safer and easier to maintain
over time,” says Smith.
One of the biggest benefits offered by the
company’s pipe launders is their durability.
Smith says some of the company’s instal-
lations in the mineral sands production
environment have lasted for up to nine years
in highly corrosive coastal environments.
What is more, they are easy to maintain.
Their design incorporates a replaceable
polyurethane boot inside the pipe that
endures wear and
protects the inside of
the pipe.
“In arduous ap-
plications, such as
those found in min-
eral sands and iron
ore mining, the boots
would have to be re-
placed about every
two to three years,” he
says, adding that the
boot can be replaced
within five minutes.
Manufactured from a
much lighter material
than steel and having
a smaller outside diameter, Multotec pipe
launders are easier to handle and can be
installed by two men without the need for
any lifting or hanging equipment.
The launder pipes supplied to chrome
producers have an outside diameter of 200,
255 and 400 mm. Every pipe launder,
installed from the collection point leading
down to the sump, had to be specially
designed and manufactured to fit into the
existing footprint of the plant.
It may just be that more chrome miners
will come to experience and appreciate the
benefits of a better pipe launder system,
thanks to Multotec.
q
Two Conturbex centrifuge installations dewatering glaubersalt and mixed salts produced using a ZLD process.
The cleaner concentrate, rougher concentrate and tail pipe launder
arrangement, together with Multotec distributors.
Siebtechnik Conturbex centrifuge is an
important feature, which enables inde-
pendent adjustment of the scroll and
drum speed. This allows adjustment
where extreme process conditions exist
and this flexibility enables performance
to be optimised.
The centrifuge is engineered in such
a manner so as to enable easy mainte-
nance and one of the features relevant
to this is the single bearing overhang
design, which allows easy access to the
internal rotating components. This saves
time, leading to greater cost effectiveness
during planned maintenance activities.
Another important time saving feature
is that cleaning nozzles, strategically
positioned within the machine, facilitate
cleaning-in-place (CIP) during scheduled
maintenance shutdowns.
Pointing to applications where
Conturbex centrifuges are operating
successfully, du Plessis says that in the
petrochemical sector these centrifuges
replaced pusher centrifuges as part of
a de-bottle necking project with the
added benefit of less frequent washing
requirements. Also in the petrochemical
industry, Conturbex centrifuges are used
to produce a sodium sulphate by-product
from a sulphur effluent stream.
Du Plessis says that there are defi-
nitely applications where the features of
pusher centrifuges will outweigh those
of the Conturbex centrifuge, however
the ZLD process is not one of these.
“We manufacture all types of centrifuges,
including pusher centrifuges, and will
recommend the correct type of centri-
fuge for the application at hand. Pusher
centrifuges are suitable for applications
where the need for crystalline purification
is essential.”
Conturbex centrifuges are also used
for water treatment and de-watering of
mixed salts, including sodium sulphate in
a colliery plant, and in a crystalliser plant
de-watering mixed salts at a platinum
operation.
q