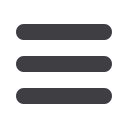

Mechanical Technology — May 2016
15
⎪
Proactive maintenance, lubrication and contamination management
⎪
B
MG’s efficiency drive, which
is designed to help compa-
nies reduce energy consump-
tion and optimise production,
encompasses predictive maintenance
services of condition monitoring and oil
analysis.
“The introduction of a structured
maintenance management programme,
which can be implemented in-house, or
partially out-sourced to a professional
organisation, is critical to maximising
production efficiencies,” says Wayne
Holton, fluid technology manager, BMG.
“The effects of friction and the resulting
wear of moving components are signifi-
cantly reduced by effective lubrication.
“Through a wide range of energy effi-
cient products – which includes synthetic
oils, lubricants and bespoke lubrication
systems – and the support of a techni-
cally competent team, BMG ensures
efficient maintenance, extended life of
components and energy savings in any
environment.
“To achieve optimum performance
and extended life of components such
as bearings and industrial chain, correct
lubrication is as important as the appro-
priate selection of each part. Although
general multipurpose grease is adequate
in many applications, more arduous
operating conditions demand the care-
ful choice of the correct lubricant and
lubrication system.
“In selecting the right lubricant for
a specific application, factors to be
considered are speed, ambient tempera-
ture, load, vibration and environmental
conditions.”
BMG’s specialist technical resources
division offers an oil analysis service
which consists of laboratory based
sampling and analysis, as well as onsite
analysis and filtration and flushing. Other
services include technical applications
consulting, product and system design,
product quality control and assurance,
as well as condition monitoring services.
Conditioning monitoring identifies
lubrication problems, misalignment and
vibration troubles and also helps in iden-
tifying the causes of the damage so that
BMG’s efficiency drive, which is designed to help compa-
nies reduce energy consumption and optimise production,
encompasses predictive maintenance services, including
condition monitoring and oil analysis.
BMG has extended its range of lubrication products to include a
single point lubricator, where the grease is pressurised by a gas
generated unit to provide continuous, reliable, clean and precise
lubrication.
Structured maintenance
management
Structured maintenance management programmes “are critical to
maximising production efficiencies,” says Wayne Holton, fluid
technology manager, BMG, while outlining his company’s
predictive maintenance service offering.
units can be fixed before further
destruction occurs. This means
reduced downtime, efficient
production and substantial cost
savings.
BMG has extended its range
of lubrication products to in-
clude a single point lubricator,
where the grease is pressurised
by a gas generated unit, to provide
continuous, reliable, clean and precise
lubrication.
These lubricators ensure less fric-
tion, which means energy savings and
extended service life of components
and equipment. Other benefits include
reduced risk of contamination and ac-
cidents, particularly in dangerous
areas; shorter maintenance times;
improved reliability of industrial
equipment and lower operating
costs.
BMG’s automatic lubricators
– which ensure exactly the cor-
rect lubrication, with the correct
grease – are easily integrated into
various applications, without the
need to modify installations.
Specially designed OMSA
lubrication systems eliminate the
risk of excessive or inadequate
lubrication and ensure the con-
stant and regular lubrication of
bearings. These systems are ideal
for use in humid and corrosive
environments.
Various greases are available
for different applications. For
example, a general purpose grease is
suitable for industrial use; heavy duty
grease is recommended for high load
applications in humid environments and
high temperature grease is designed for
long term lubrication at high tempera-
tures, up to peaks of 175 °C.
A synthetic oil is available for high
temperature chains and a multi-purpose
grease, which complies with food and
pharmaceutical standards, is used for
bottling machines, dairy equipment and
in food manufacturing.
BMG now has 140 mobile techni-
cians with specialist technical skills and
equipment to conduct breakdown and
routine maintenance on plant. This team
carries out trouble- shooting and advises
on possible productivity improvements,
to ensure the highest level of plant output
and reliability.
Specialist services include instal-
lation, adjustment, replacement and
maintenance of components, shaft and
pulley alignment, balancing, condition
monitoring, oil sampling and analysis
and critical equipment inspections and
lubrication schedules. Maintenance
training and fault diagnosis also form an
important part of BMG’s field services.
q