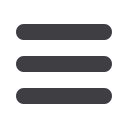

Mechanical Technology — May 2016
11
⎪
Proactive maintenance, lubrication and contamination management
⎪
industry:
a different approach
SKF’s new
Food Line family
T
he SKF Food Line family includes
19 different standard sizes of deep
groove ball bearings from SKF’s ex-
tensive range, in diameters ranging from
8.0 to 40 mm.
“Both the blue seal and the lubricant
were developed for use in food and beverage
applications,” says David Oliver, SKF Europe
industry manager Food and Beverage. “The
overall bearing meets the highest standards
of food management systems and regula-
tions. This offer is unique to SKF, none of our
competitors can offer the full package of food
grade grease, plus FDA and EC approved
blue coloured sealing in their stainless steel
deep groove ball bearings.”
Food safety management systems such
as HACCP are placing greater importance on
safe food production. This means that com-
ponents used in production should be either
food-safe or detectable. Many food product
recalls are initiated due to the possible
presence of hard or sharp objects so food
safety and detectability are high priorities
for any components operating close to the
food stream. The same is true of lubricants.
For this reason, food-grade lubricants are
increasingly used on a plant-wide basis to
prevent the chance of applying non-food
greases to a critical part.
SKF’s stainless steel deep groove ball
bearings offer high resistance to corrosion,
so that they can withstand the aggressive
wash down regimes that are necessary in
the food industry. The special seal enhances
this, helping to retain lubricant and prevent
ingress of wash down fluid.
q
Above:
The traditional wash down and relubrication cycle presents risks to both bearing
service life and the environment.
Left:
In the food industry, for processing fish, for example,
SKF has developed solutions that fulfil FDA and EC requirements. These bearings feature
Re-lubrication free bearing technologies; high efficiency seals that keep lubricants in and
contaminants out; and the use of corrosion resistant stainless steel materials.
wastewater stream or disposed of using
grease cleaning wipes.
At the starting point, operators should
proactively assess costs, risks, opportuni-
ties and benefits of managing lubrication
as a broad strategy.
At SKF, we have found that a techni-
cal assessment of a production process
provides the structure to readily identify
potential issues, risks, opportunities and
benefits in moving from current ap-
proaches. And the good news is that it
does not require much time and from
the assessment results, it is usually easy
to plan short, medium and long-term
activities.
Challenge the ‘always done it this
way’ attitude
Identification of potential negative im-
pacts on HACCP can lead to areas for
improvement where SKF offers a range
of technology and service offerings dedi-
cated to helping to manage lubrication.
These cover for example
• Re-lubrication free bearing technolo-
gies.
• High efficiency seals that keep lubri-
cants in and contaminants out.
• Lubrication management: we can re-
view and optimise lubrication strategy
and lubrication routines in or-
der to: apply correct amounts
of lubricant at correct intervals, either
manually or through automatic dis-
pensing systems; use correct tools
that allow correct methods to be
followed; and set up an appropriate
training programme for maintenance
technicians and operators.
• SKF can also offer smart ways to
detect poor lubrication condition
by analysing vibration data through
‘vibration parameters’.
There are different ways to meet these
challenges. “At SKF we can offer more
than the traditional lubrication man-
agement approaches that look only at
lubricants and the way to apply them.
We can bring technologies that take away
the need to re-lubricate, adding value
from a food safety, cost, reliability or
environmental perspective. What makes
the difference is our deep knowledge of
rotating equipment, industry experience
and commitment to reduce costs of own-
ership,” Backer concludes.
q