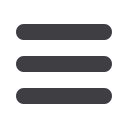

18
Mechanical Technology — May 2016
⎪
Materials handling and minerals processing
⎪
W
ith the increased focus
on environmental legis-
lation and the need for
companies to comply with
ISO 14001 it has become critical for
process plants to deal effectively with
effluent streams. This typically involves
the introduction of zero liquid discharge
(ZLD) processes at the back end of exist-
ing process plants.
ZLD is used across a number of indus-
tries including mining, pulp and paper,
chemical processing and the petrochemi-
cal sector. Its application is typically to
evaporate and concentrate an effluent or
waste stream. It is also sometimes used,
however, to produce a saleable product.
The process involves a suite of equipment
from Multotec including dewatering cen-
trifuges and CleanTeq solvent extraction.
Gerrit du Plessis, product specialist
for solid/liquid separation at Multotec
Process Equipment, explains that be-
cause ZLD is always at the end of a
process flow, the equipment used is
generally subjected to extremes such
as the chemical composition concentra-
Centrifuges
for achieving
zero liquid discharge
A Conturbex centrifuge dewatering glaubersalt product in a ZLD plant.
In this article, Multotec Process Equipment’s Gerrit du Plessis describes
the role of Conturbex centrifuge installations in zero liquid discharge (ZLD)
applications at the back end of existing process plants.
tion in the slurry and how its flow rate
fluctuates.
“Due to both these issues, it is es-
sential that the equipment selected for
the ZLD process is capable of dealing
with these varying factors, while still
effectively producing the desired end
result,” he says.
“Often, where engineers have only
previously known and used pusher cen-
trifuges they may not be aware that there
is an option that is far more suited to
the ZLD process. And more importantly,
one that will provide significant benefits,
including more reliable performance with
associated cost savings,” Du Plessis
adds.
He recommends that those imple-
menting the ZLD process ensure that
they have access to an OEM that under-
stands the entire process and is able to
take all factors including flow rate, solids
concentration, temperature, particle size
distribution, chemical composition and
corrosive properties into account.
There is an extensive global reference
base of successful Siebtechnik Conturbex
centrifuge installations in ZLD applica-
tions, with some 7 000 machines in
more than 1 000 applications across a
spectrum of industries. Multotec markets
this range of centrifuges in southern
Africa, and du Plessis says it has the
requisite depth of minerals processing
knowledge and ability to assess any given
application and to provide a customised
solution capable of meeting process
expectations.
He says the Siebtechnik Conturbex
centrifuge offers a number of major
advantages in the ZLD process. “Chief
amongst these is significantly increased
reliability as the machine is designed for
a short product residence time, which
means that its performance is not im-
pacted by the fluctuating flow rate or
fluctuating concentration of solids.”
The Siebtechnik Conturbex centrifuge
has been engineered with a scrolled
product transporting mechanism that
distributes the solids product evenly
across the basket. This allows vibration
free operation ensuring better mechanical
integrity of the equipment.
“This is an important feature as
uneven distribution during this process
results in increased stresses on the
components, with eventual mechanical
failure. Unplanned downtime as a conse-
quence of this sort of stress would have
serious knock on effects for the plant,
as well as a significant environmental
impact,” he explains.
A third major benefit is that the
machine is self-cleaning. This feature
is particularly relevant during a power
outage or stoppage on the plant. When
this occurs, the rotating components slow
down while simultaneously cleaning the
basket. This then allows the machine to
be restarted without the need to do any
form of manual cleaning. Significantly,
this feature is unique to the Conturbex
machine.
Materials of construction are always
important when equipment operates
in extreme conditions, as this ensures
durability and optimum component life.
Where extremely high temperatures and
highly corrosive elements are found in the
effluent being processed, specialised ma-
terials of construction are recommended.
And in applications subjected to harsh
abrasion, abrasion resistant materials are
applied to the flight of the scroll to ensure
long life of both the rotating components
and the centrifuge itself.
The double drive functionality of the