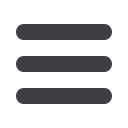

D
rilling,
P
iercing &
P
unching
T
echnology
M
arch
2009
www.read-tpt.com82
›
features of this machine are pitches
precision, straightness of the worked bars
and fast tooling change. The operator is
just required to load the piece into the
machine at the right position and push
the start buttons. When all operations
are over, the operator has to unload the
finished tube and reload the machine.
The machine is constructed from a heavy
electro welded steel frame, a trolley
equipped with special clamping gripper,
special punching units, controlled axis to
manage all tube movements, a hydraulic
power pack, and an electrical cabinet
supplied with control push panel and
electrical installation on board.
The main technical features are a maximum
tube size of 80mm, a standard length of 3m
(options for 4/5/6mt), and a punching power
of 3/6/10 ton.
There is also a maximum bar feeding
speed of 40mt/1', a position accuracy of
0.1mm/mt, a gripper rotation of 90° for
round tube, pitches and lengths settings
directly from a panel board, and an
optional controlled gripper rotation and
automatic loader.
SMS Engineering Srl
– Italy
Fax
: +39 035 581509
:
commerciale@sms-italy.itWebsite
:
www.sms-italy.itdeformation. It is designed for shelving,
radiators, ladders, bed frames and
similar products. Punching can be
undertaken on one side, two opposite
sides or alternate opposite sides (pitch
is variable).
The machine is capable of punching
one or more holes every time. The main
SMS Engineering, Italy, has launched a
new automatic punching machine, branded
PSA-50. This simple machine is suitable
for punching steel, stainless steel and
aluminium tube and bars with round, square
or rectangular section.
The PSA-50 can produce round
and square holes, with or without
New automatic punching machine type PSA-50
environmentally friendly emulsion thereby
extending tool life.
Both drilling units are fitted with a multi-
spindle boring head and work with both fast
and operational speeds. The high speed
milling head is fitted with a hard metal
tipped disc cutter.
A conveyor belt is fed by a chute to dispose
of the punched cut outs and bored and
milled swarf. The aluminium profiles are
clamped on the head side by a collet fixing
carried on the feed measuring carriage and
timed from a CNC-linear feed.
As the profiles are partly anodized – and
must remain entirely free of scratches – felt
edged lowering rollers are fitted between
the punching units. A Siemens 810T
system controls the operation and storage
programs for running and storage.
Friedrich Petig GmbH
– Germany
Fax
: +49 218 173 108
:
info@petig.comWebsite
:
www.petig.commachines that utilise the through-punching
method, and also combine drilling and milling.
Petig’s machines work to punch heating
holes in the profiles, with boring of sunken
holes and milling of slots. The completed
profiles
are
then
matched
together
with assembly of
the heating and air
conditioning channels.
The hydraulic impact
punch unit allows
differing
punching
pressures between
200-315kN. Column
mounted tools enable
punching of non
uniform shapes. At
predetermined
and
adjustable distances,
the stamped holes
are sprayed with an
High volume aluminium profiles, such as
those used in the manufacture of luxury
travel coaches, can be efficiently produced
with a combined machine for drilling, milling
and punching. Friedrich Petig, Germany,
manufacture a range of tube punching
The new PSA-50 punching machine from SMS Engineering
Drilling and punching of aluminium sections
Friedrich Petig supply the technology for drilling, milling and punching