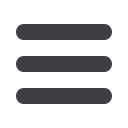

D
rilling,
P
iercing &
P
unching
T
echnology
M
arch
2009
www.read-tpt.com84
›
With proper tooling, many of the previously
mentioned problems can be eliminated or
at least minimized. There are several bit
profiles available that greatly reduce burrs
and speed the drilling cycle. Added to this
is tooling designed to stabilize and guide
the bit during the drilling cycle, which leads
to higher accuracy. As with the punching
process, it is advantageous to index the
tube under the fixed position of the drill.
Both manual and automatic equipment
are produced for making accurate linear
and radial indexes. Manual style punch
machines rely on an operator to make the
different stops at each pattern location and
to cycle the punch at each stop.
A manual machine is relatively inexpensive
and can be customized for a wide variety
of tube materials, shapes, and sizes.
Automatic machinery that is built for this
process relies on a servo based positioning
system that is driven by a part program to
make the intended pattern stops and to
cycle the punch at each stop.
While an automatic machine of this type is
more expensive, it makes up for the added
cost with increases in speed, accuracy,
and efficiency. An automatic machine is
also better suited to producing complicated
patterns that contain many linear and radial
locations.
Machinery for either process should
be simple to set up and provide a fast,
accurate method for getting from one hole
to the next. A hole making machine must be
rigid and provide nearly perfect, repeatable
alignment between the tool and the hole –
especially when mandrel punching.
The choice for machinery and tooling, and
ultimately the hole making process, can
be a difficult one. Punching and drilling are
virtuous because they are simple processes
and offer a very low cost per hole. There
are limitations to each, but with a good
part design that is based on the processing
method, most limitations can be overcome.
Carson is the manufacturer of a line of hole
punching equipment for the production of
header tubes. These machines come in two
basic versions, manually operated and semi-
automatic. The company also offers a range
of equipment for bending, end forming, end
closing and other special machines.
Carson Engineering & Mfg
– USA
Fax
: +1 479 751 2834
:
info@carsonengineering.comWebsite
:
www.carsonengineering.comfree and creates very little distortion to the
tube’s original shape. As an added bonus,
the waste that is produced is a slug that is
easily evacuated from the point of operation
and gathered for recycling.
Another advantage of the mandrel punching
process is that it allows for the punching of
different shapes. This ability is essential to
many applications. The preferred method for
producing a pattern of holes with this process
is to index the tube over a fixed mandrel.
This method allows for a very accurate
punch to mandrel alignment, which is
essential for maintaining the quality of the
punched hole.
There are situations where a mandrel
punched hole is not an option. These
include cases where it is impossible to
insert a mandrel due to a feature of the
tube and, more commonly, the case where
the hole size is too near the inside size of
the tube. In this case, a mandrel would be
too fragile for practical use and would not
allow the necessary clearance needed for
slug evacuation.
When these situations arise, a drilled hole
is a very good option. The main drawbacks
normally associated with drilling are burrs
around the hole, chips, and a reduced rate
of production compared to punching. There
is also the fact that a drill can produce
round holes only.
When faced with the task of producing a
pattern of holes in tubing, there are many
different options to consider. There are
mandrel punched holes, mandrel-less
punched holes, drilled holes, milled holes,
pulled (or collared) holes, and others. For
most applications, the best options are
mandrel punched holes or drilled holes.
Mandrel punching is generally favoured
over any other because it is clean,
accurate, and fast. This process utilizes
an internal die or mandrel, an external
punch, and a tube support. When tooled
properly, a mandrel punched hole is burr-
Special robot loading device for punching lines
Apollo, Italy, has introduced a robotic loading device that works in unison with the
company’s Twin punching lines. The robot device can load and unload workpieces from
dedicated containers to the machine and back again. This robot considerably lowers
working time and labour.
The robot can simultaneously load two punching lines or take the cut material from a
sawing machine coupled with an Apollo punching machine. The time for loading and
unloading is approximately 6 seconds.
The punching line features remain the same, as the coupling with the robot does not
involve any technical change. Apollo can provide customized solutions in order to
transform all of its punching lines into fully automatic machines. Alternatively, the
company can provide the robot coupled with the new punching machines.
Apollo may also be able to supply overhauled robots of the KUKA and ABB brands.
Apollo
– Italy
Fax
: +39 0536 851273
:
info@apollosrl.comWebsite
:
www.apollosrl.comExpertise in tube punching and drilling technology
Mandrel punching is generally favoured because
it is clean, accurate, and fast