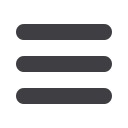

M
ay
2009
www.read-tpt.com116
›
A study into rollforming of
parabolical section
By Dr Jiying Liu, Mr Yuanguang Li and Mr Zhengqing Ai, North China University of Technology, Beijing, China
Supported by Beijing Municipal Natural Science Foundation (3082008)
Abstract
In order to meet precision requirements, the parabola fitting is
achieved by using the smallest arc. Based on the Biswas formula,
the springback model of rollforming parabolic section is a viable
option. It is possible to design the roll flower pattern of parabolic
section. The correctness of the springback model is verified by
experiments and finite element analysis. The rollforming method
can be used for the manufacture of parabolic section in engineering
applications.
Key words:
Parabolic section, rollforming, FEA simulation, Biswas
springback
1. Introduction
Directional light, which is normally present in sectional surface, can
be focused on the focal line by use of a parabolic section. It can
then achieve a highly efficient gathering that puts heat pipe on the
focal line. Based on this feature, parabolic section can be used as a
reflector of solar energy water heater.
The principle drawing is shown in figure 1. Some research shows
that heat energy efficiency of multiple parabolic reflector (composed
of parabolic section), is higher than that of a plane and circle arc
reflector by 60 to 70 per cent
[1] [2]
.
At present, because of
high cost and difficult
forming,
to
some
extent, application of
parabolic
section
is
limited in engineering.
Roll forming is a high
production and low cost
of forming process of
sheet metal. So, using
roll forming technology
to manufacture parabolic
section has positive
signification to industrial
application.
The difficulty of using roll forming technology lies in manufacturing
the section of variable curvature, what with the complexity of
spring back during forming which can not be resolved by existing
technology. Aimed at reflector of solar energy water heater and
combining finite element simulation and experiment analysis,
we have investigated a roll forming method to form parabolic
section.
2. Forming of a parabolic section
In this study, an inside contour of parabolic section is used as the
research object. The mathematical expression of the contour is
The section material is 1060H18 aluminium sheet. The unfolding
width of the section is 120mm, and the thickness is 0.5mm.
Using a circle arc subsection fitting parabolic line, the variable
curvature problem is simplified as a multi-arc problem. When
experiencing a normal error with a maximum limit of less than
0.1mm, the parabolic section can be substituted with 4 arcs. Two
outside arcs are formed first, and then two inside arcs.
Due to this fact, forming with a large radius of thin wall, the
springback must be considered. For fitting a circle arc, the over-
bend forming method should be applied, and the over-bend radius
is calculated by the following formula
[3]
:
(where,
r
f
=
,
r
i
1
= bend radius (mm),
r
i
2
= radius after
springback (mm),
r
f
= yield curvature (mm),
E
= Young’s modulus
(MPa),
t
= thickness of sheet materials (mm),
S
= yield stress of
materials (MPa))
The roll flower pattern is shown in figure 2. It is possible to see that
the third pass is an over-bending forming of the outside arc, and the
ninth pass is over-bending forming in the side arc.
3. Experiments and result analysis
According to the forming of the flower pattern, the rolls were
designed and manufactured, and the experiment carried out by a
rollforming machine at the North China University of Technology
Roll-forming Laboratory (figure 3). The precut length of the
aluminium strip was 1,000mm, width 120mm and thickness 0.48mm.
The formed parabolic section samples are shown in figure 4.
Figure 1
:
Principle drawing of solar energy
reflector with parabolic section
Figure 2
:
Roll flower pattern
1
72
y
=
x
2
,
(–48 ≤
x
≤ 48)
=
1–1.5
•
+
0.5
•
3
r
i
1
r
i
2
r
i
1
r
f
r
i
1
r
( )
E
×
t
2
×
S